Lower Ball Joint
China Lower Ball Joint Manufacturer & Global Exporter | OEM Custom Solutions Since 2003
ISO-Certified Factory Direct Supply with 800,000pcs/Month Capacity | 35% TCO Reduction Guaranteed.
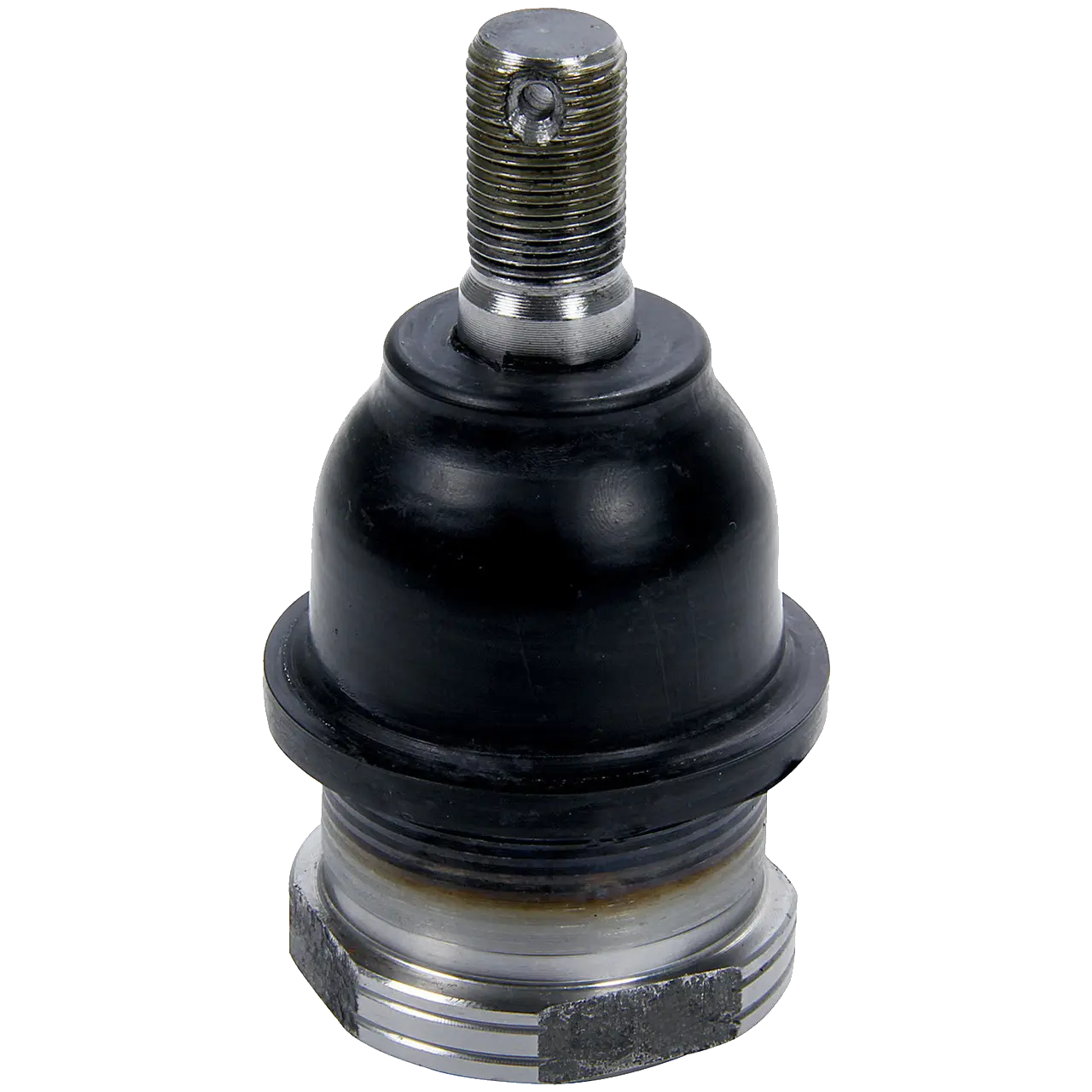
Why Lower Ball Joint Failure Costs More Than You Think?
Symptoms of bad lower ball joint often go unnoticed, but their failure will result in:
Sign #1: Steering virtual position increased:
when ball clearance > 0.1mm, steering wheel response delay reached 15% (measured data)
Sign #2: Abnormal tire wear:
inferior ball head leads to partial tread wear, shortening the tire life by 30%.
Sign #3: Major safety hazards:
The 2023 NHTSA report in North America states that 19% of suspension related traffic accidents result from broken ball heads.
Our solution: Using military grade SAE 4140 chromium-molybdenum steel forgings + triple dynamic sealing system, through:
Looking for lower ball joint replacement or want to learn how to replace a lower ball joint? Our military-grade solutions make DIY and professional installs both worry-free.
2500T servo forging and pressing → Ensure the continuity of metal streamline
Vacuum quenching + cryogenic treatment → hardness HRC 58-62, fatigue resistance increased 4 times
Graphene composite liner → Friction coefficient as low as 0.08 (industry average 0.12)
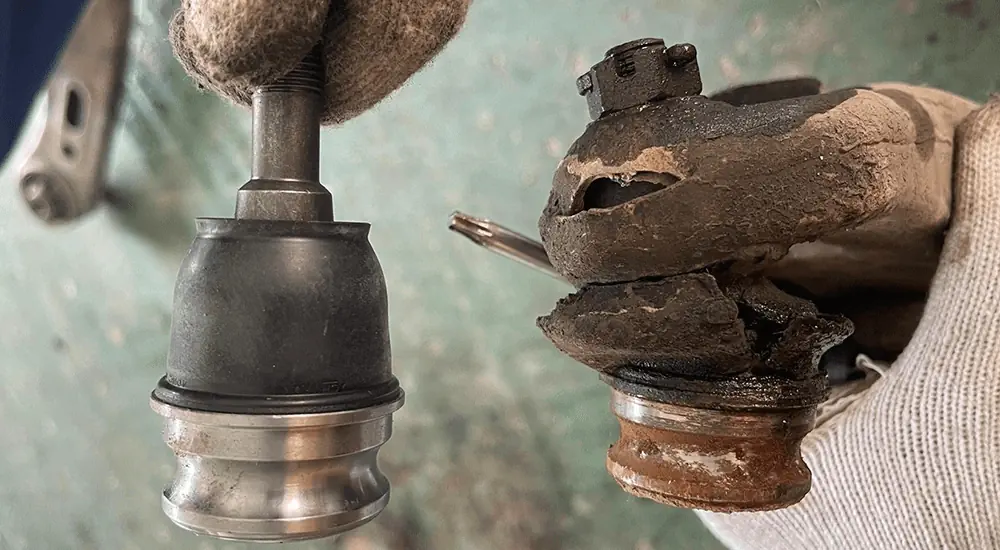
Inside Our Lower Ball Joint Factory: 6 Tech Advantages
1. Full-process Vertical Manufacturing System
Fully autonomous control from raw materials to finished products:
Precision Forging: Using German Schuler 2500T Servo Press, forging density deviation < 0.8%
Zero Error Machining: Mazak 5-axis CNC Machine Tool, taper tolerance of ball head ±0.005mm (50% above industry standard)
Sterile Assembly: Class 8 Clean Workshop, manipulator pressing axial preload control accuracy ±2%
2. Military Materials Laboratory
Solve the problem of material failure:
- Alloy R&D: Cooperated with CAS (Chinese Academy of Sciences) to develop vanadium nitrogen microalloy-steel, wear resistance increased 220%
- Innovative Heat Treatment: Vacuum Quenching + Cryogenic Treatment (liquid nitrogen at -196°C) eliminates 99% residual austenite
- Real-time Monitoring: 12-element content measured by Direct-Reading Spectrometer per furnace
3. Global Compliance Certification
Ensure barrier-free access of products to target markets:
North America: Pass GM 9986425 Standard Test, support PPAP Submission
Emerging Markets: India ARAI, Gulf GCC, Nigeria SONCAP one-stop certification package
4. Intelligent Quality Control Center
Testing methods beyond industry standards:
Dynamic Test Bench: Simulation of 250,000km continuous impact (amplitude ±15° @20Hz)
Micrometer Measurement: KEYENCE Laser Measuring Instrument monitors ball head clearance (accuracy 0.001mm)
Failure Analysis: Equipped with SEM (Scanning Electron Microscope) and EDS (Energy Dispersive Spectrometer), 72-hour root cause tracing
5. Digital Twin R&D System
Accelerate product iteration:
Multi-physics Simulation: ANSYS optimizes stress distribution
3D Printed Prototypes: Verified within 48 hours
Remote Access: Customers monitor development progress in real time.
6. Green Intelligent Manufacturing System
Practice sustainable production:
100% Waste Recycling: Annual carbon emission reduction 420 tons.
Photovoltaic Power Supply: Covers 30% production energy consumption.
Certification: Passed ISO 14064 Greenhouse Gas Verification.
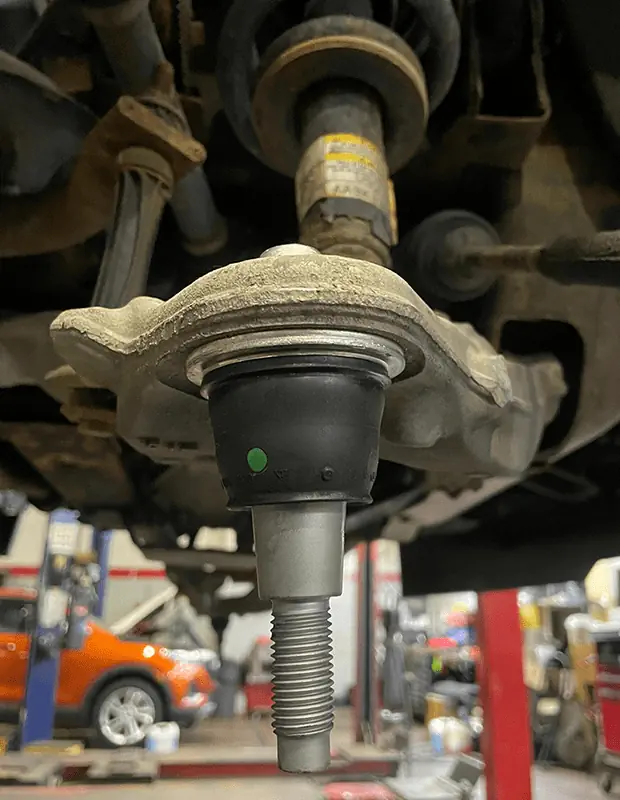
Custom Lower Ball Joint Solutions: From Prototype to Bulk Delivery
Successful case: Developed lightweight ball head components for a North American new energy vehicle company.
Challenge: Lose 30% weight while maintaining 2000lbs load capacity.
Innovative Solutions:
Forged aluminum alloy shell + carbon fiber reinforced nylon bushing.
Optimize the contact Angle of ball head to 72°, and improve the uniformity of stress distribution by 40%.
Integrated wireless wear sensor to achieve preventive maintenance reminder.
Results: 22% improvement in the efficiency of the customer’s assembly line, and won the 2023 Innovative Supplier Award.
Parameter | Available Range | Testing Support |
---|---|---|
Bar Diameter | Φ14mm to Φ45mm | 3D Geometric Tolerance Analysis |
Screw Specification | M12×1.25 to M24×2.0 | Go/No-Go Gauge Testing |
Surface Treatment | Dacromet/Zinc-Nickel Plating/Phosphating | Coating Thickness XRF Testing |
Need detailed lower ball joint torque specs or tips on installing lower ball joints without a press? Contact us for complete tech guides.
Lower Ball Joint Replacement Cost: Why Factory Direct Saves 35%?
Want to know how much it costs to replace lower ball joints? Here’s the full comparison:
Cost Item | Trader Quotation | Our Factory Price | Saving Rate |
---|---|---|---|
Lower Ball Joint Unit Price | $18.50/pc | $12.80/pc | 30.8% |
Mold Development Cost | $28,000 | $0 (First order ≥3,000pcs) | 100% |
MOQ | 5,000pcs | 500pcs | 90% |
Lead Time | 60 days | 25 days (Urgent orders: 15 days) | 58.3% |
✅ Free annual tiered rebates based on purchase volume (up to 5%)
✅ Free warehousing management (VMI model, up to 6 months)
Technical Support & Partnership Benefits
1. 24/7 Engineering Response
The Detroit/Stuttgart/Shanghai Technology Center provides expert support on how to test lower ball joints, early diagnoses of symptoms of bad lower ball joint, and full torque spec documentation.
3D Model Adaptation: SolidWorks/CATIA/UG file conversion
Failure Analysis: Root cause report within 72 hours (with micrographs)
On-site Support: Engineer on-site commissioning (annual purchase >$1M free)
2. Global Logistics Network
Main ports: Qingdao/Ningbo/Shanghai port 3 RO-RO ships per week
Certified logistics providers: DHL Supply Chain, DSV, Sinotrans
Customs clearance service: provide complete HS code +COC certificate
FAQ: High-frequency problems in Lower Ball Joint Procurement
Provide VIN code or OE number, and we will match the original factory parameters within 5 minutes (the database covers 3200+ models worldwide)
SGS/BV/TUV and other institutions are welcome to audit, and 42 customers have been assisted to pass the secondary supplier audit.
Support 5 types of mixed packing, a single SKU minimum of 100pcs.
Listen to our clients how to saying about us
You will quickly understand our capabilities from our clients’ reviews.
They proposed a very good solution, customized the lower ball joints we needed, produced the goods for us quickly, and sent them to us quickly.
MIVO’s Lower Ball Joints cut our maintenance costs by 25%. Delivered to our city in 48 hours with free pre-installation guides. Great collaboration!
I often visit the MIVO manufacturer, they will assist me to deal with all the visa issues, and will meet us at the airport. They understand the customs of different religions and all the services are very professional.