Control Arm Bushings
Your one-stop control arm bushing supplier – MIVO Manufacturer
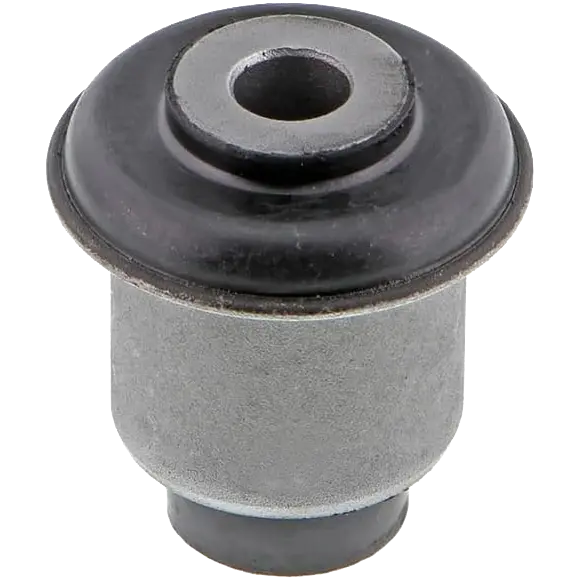
Control Arm Bushing Types by Position & Key Functions
-
Upper control arm bushing
linking it to the frame or suspension. It helps maintain wheel alignment, dampens noise, and ensures smooth articulation during suspension travel.
-
Lower control arm bushing
A rubber or polyurethane component that cushions the connection between the lower control arm and the vehicle’s chassis. It absorbs road shocks, reduces vibration, and allows controlled movement for steering and suspension.
-
Front control arm bushing
A bushing used in the front control arms of a vehicle’s suspension system. It stabilizes the front wheels, manages steering precision, and absorbs impacts from bumps or uneven terrain.
-
Rear control arm bushing
A similar component in the rear suspension, connecting rear control arms to the chassis. It supports rear-wheel stability, reduces road noise, and handles forces during acceleration or cornering.
Control Arm Bushing Materials & Typese
-
Bushing Hydraulics
linking it to the frame or suspension. It helps maintain wheel alignment, dampens noise, and ensures smooth articulation during suspension travel.
-
Rubber Bushing
A rubber or polyurethane component that cushions the connection between the lower control arm and the vehicle’s chassis. It absorbs road shocks, reduces vibration, and allows controlled movement for steering and suspension.
-
Polyurethane Bushing
A bushing used in the front control arms of a vehicle’s suspension system. It stabilizes the front wheels, manages steering precision, and absorbs impacts from bumps or uneven terrain.
-
Spherical Bushing
A similar component in the rear suspension, connecting rear control arms to the chassis. It supports rear-wheel stability, reduces road noise, and handles forces during acceleration or cornering.
OEM Control Arm Bushing Manufacturer | China Factory Direct
Six Core Competencies: Certification & Quality Assurance
Certification
1IATF 16949, ISO 14001
Testing Capability
23D Profiler and fatigue testing machine
R&D Strength
3Patented technology (corrugated structure design)
Production Traceability
4Laser coded for full traceability
Delivery Speed
572-hour urgent order response
Technical Support
6FMEA analysis report and installation training
20 Years of Expertise in Control Arm Bushing Manufacturing
With over 20 million control arm bushings delivered worldwide, we support top-tier luxury vehicle manufacturers across more than 30 countries, ensuring industry-leading standards.
Complete industry certification: IATF 16949, ISO 14001 certification, in line with European and American environmental standards (RoHS/REACH).
Quick response ability: the engineer team is online 24 hours a day, supporting cross-time zone technical docking (including German, English and Russian services).
2000㎡ constant temperature workshop: precision manufacturing to ensure quality
Fully automated production line: using German KraussMaffei injection molding machine + Japan Fanac CNC machine tool, tolerance control ±0.01mm.
Strict environment control: workshop constant temperature (25±2℃), humidity ≤30%, to ensure the stability of rubber curing.
Monthly production capacity of 500,000 sets: support large volume orders (one-day peak production capacity of 20,000 sets), emergency orders delivery within 72 hours.
12 patented technologies: innovation-driven industry benchmark
-
Shock absorber corrugated structure
Innovation: Multi-layer corrugated design to disperse stress, prolong life 300%, has been applied to Mercedes-Benz GLC suspension system.
-
Triple temperature domain compensation technology
Breakthrough: elastic modulus fluctuation < 5% in extreme temperature range of -60℃~180℃, suitable for models in alpine/desert areas.
-
Conductive bushing technology
Application scenario: eliminate electromagnetic interference of electric vehicle motor, and obtain exclusive procurement certification of a European electric brand.
-
Bimetallic anti-rust coating process
Advantages: COPPER + stainless steel composite coating, salt spray test 2000 hours without corrosion, specially developed for coastal areas.
-
Multi-stage buffer hydraulic chamber
Design highlights: three-stage hydraulic oil circuit, shock absorption efficiency increased by 40%, Range Rover models with standard technology.
-
Quickly install the buckle structure
Efficiency improvement: pressure-free design, shortened replacement time to 15 minutes, reduced aftermarket repair rate by 60%.
-
Nano reinforced rubber formula
Performance breakthrough: adding carbon nanotubes, the tear strength is increased by 80%, and the life span reaches 2.5 times of the industry standard.
-
Adaptive damping system
Intelligent adjustment: automatically adjust the hardness according to the vibration frequency of the road surface.
-
Modular bushing design
Compatibility: the same substrate is suitable for 5 models, reducing the number of SKUs by 70% and the inventory cost by 45%.
-
Ultra-low temperature vulcanization process
Environmental protection innovation: vulcanization temperature reduced to 80℃, energy consumption reduced by 30%, through the EU REACH environmental protection certification.
-
Stress visualization monitoring technology
Intelligent warning: built-in optical fiber sensor, real-time transmission of bushing deformation data to the car computer.
-
Self-healing rubber material
Black technology: microcapsule sustained release technology, slight cracks can be automatically filled and repaired, extending the life by 50%.
OEM/ODM customization: full-link service from demand to mass production
Flexible customization process:
① 3D scanning original sample data → ② CAE simulation optimization → ③ 150 hours bench test → ④ road test certification → ⑤ mass production.
personalized service
✔️Brand customization: support LOGO laser engraving, independent packaging design.
✔️Function upgrade: Sensor interface can be added to realize intelligent monitoring of bushing life.
✔️Formulation optimization: Develop anti-corrosion coatings for regions with high salt spray, such as the Middle East.
✔️Free sample test: provide 5 groups of comparison samples (including test report), support 48 hours rapid proofing.
Full-dimension quality control: accurate traceability from raw materials to finished products
Traceability of raw materials: self-developed formulation of rubber raw materials, sample testing of each batch (elasticity, anti-aging, hardness).
Production monitoring: laser traceability code binds each product, can query production time, operator, testing records.
Rigorous testing:
- Salt spray test for 1000 hours (far exceeding the industry standard of 500 hours).
- 3 million times of dynamic fatigue test (2.3 times of industry life).
- High and low temperature cycle test (-60℃~180℃ impact test).
Sustainable collaboration: long-term value empowerment
Cost optimization: more than 5000 sets of orders to enjoy ladder discount, long-term cooperation customers free mold fees.
After-sales guarantee: 2-year / 50,000 km warranty, providing installation video, technical manual and remote diagnosis support.
Global logistics: DDP/DAP to door service, covering sea, air, railway (Russia dedicated line 7 days).
The Ultimate Guide to Control Arm Bushings for OEM & Aftermarket Suppliers: Performance, Maintenance & Customization Insights
Reply within 2-8 hours
Via E-mail
MIVO sales and technical teams provide service 24/7
- What is a control arm bushing?
- Mainstream structure types and applicable scenarios
- Material Selection Guide
- Seven fault symptoms are fully resolved
- Self-check flow chart: four steps to accurately locate the fault
- Warning level and treatment suggestions
- Buy the gold standard
- The whole process of replacement
Core Knowledge of Control Arm Bushing: Functions, Structures & Material Selection
1).What is a Control Arm Bushing and Why is it Important?
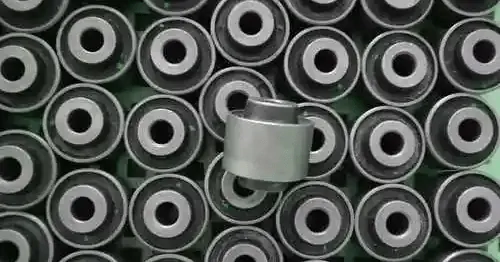
The control arm bushing is a key buffer component in the automotive suspension system. It connects the control arm with the frame and is made of rubber, polyurethane or hydraulic materials. The core functions include:
Shock and noise reduction: absorb 80%-90% road impact, improve driving comfort.
Precise positioning: ensure the geometric positioning accuracy of wheels (±0.15mm) to avoid deviation.
Prolong life: disperse stress, reduce metal parts wear, reduce maintenance costs
2).Mainstream Control Arm Bushing Types and Their Applications
Type | Material Characteristics | Applicable Vehicle Types |
---|---|---|
Hydraulic Bushing | Hydraulic oil absorbs shocks, dynamic buffering | Luxury cars, premium SUVs |
Rubber Bushing | Cost-effective and durable, excellent elasticity | Family sedans, urban SUVs |
Polyurethane Bushing | High compression resistance, oil and wear resistant | Modified cars, racing cars, high-load environments |
Spherical Bushing | Large-angle steering, high strength | Off-road vehicles, sport suspension systems |
3).Material Selection Guide
Natural Rubber (NR): The most cost-effective material for control arm bushings, ideal for ordinary road conditions (-40℃~80℃). It ensures durability and comfort in daily driving.
Nitrile rubber (NBR): strong oil resistance, preferred in the engine compartment.
Polyurethane (PU): tear resistance increased by 2.3 times, suitable for modification requirements.
Hydraulic material: dynamic buffer, suitable for luxury car complex road conditions.
Common Control Arm Bushing Fault Diagnosis & Warning Signs for Safe Driving
1).Seven fault symptoms are fully resolved
1. Abnormal sound (bumpy road “clunk” sound)
Causes: aging and cracking of rubber, corrosion of metal shell or oil leakage of hydraulic bushing
Risk: Long-term neglect may accelerate the wear of suspension ball head and shock absorber.
2. Deviation of direction (imaginary position of steering wheel > 15%)
Judgment criteria: continuous correction of direction when going straight, normal tire pressure is still offset lane.
Root cause: the deformation of bushing leads to the misalignment of the control arm and the disorder of the four-wheel positioning parameters.
3. Brake nod/tail flick (body leans forward or sideslip when braking)
Key data: when bushing looseness > 2mm, the braking distance increases by 10%-15%.
Emergency treatment: avoid sudden brake, priority low speed to the maintenance point.
4. Abnormal tread wear (inner wear > 2mm/ 10,000 km)
Typical performance: the tire is “serrated” or “unilateral wear”.
Associated fault: may be accompanied by steering tie rod, swing arm ball head wear.
5. Looseness of chassis (increased roll over bending)
Scene: When changing lanes at high speed, the body wobbles obviously, and the control confidence decreases.
Detection method: Compared with the turning posture of the new and old cars, the roll Angle increases by 20%-30% after the bushing is aged.
6. Suspension subsidence (body height asymmetry)
Measurement standard: height difference between left and right eyebrow > 10mm (no-load condition)
Hidden danger: long-term imbalance leads to uneven force on half shaft and drive shaft.
7. High frequency vibration (steering wheel/seat shake)
Working condition: the vibration is significant above 60km/h, and the damping efficiency of bushings decreases by more than 50%.
Professional tool verification: Resonance frequency analysis using chassis vibration spectrometer.
2).Self-check flow chart: four steps to accurately locate the fault
Step 1: Visual Inspection of Control Arm Bushings (No Tools Required)
Rubber status: crack length > 3mm, hardening (nail press inelastic recovery) → immediate replacement
Metal parts: shell corrosion area > 30% or deformation → risk of fracture.
Step 2: Manual test (jack required)
Press control arm: up and down swing clearance > 2mm → bushings loose and fail.
Crowbar detection: Lateral crowbar control arm, displacement > 1.5mm → loss of positioning function.
Step 3: Precision measurement (professional equipment)
Laser locator: bushing shape variable > 0.5mm → beyond the safety threshold (standard ±0.15mm).
Torque wrench: fixed bolt torque attenuation > 20% → Need to re-tighten or replace the bushing.
Step 4: Dynamic road test (comprehensive verification)
Test scene:
30km/h over speed bump → Auscultation chassis abnormal sound type (rubber friction sound/metal crash sound).
60km/h emergency lane change → Feel the body roll and direction feedback sensitivity
Data recording: OBD equipment is used to read the sensor parameters of the suspension system and compare the factory standard values.
3).Warning level and treatment suggestions
Fault Level | Symptoms | Recommended Action Timeframe |
---|---|---|
Critical | Metal noise + looseness >3mm | Stop driving and repair immediately |
Moderate | Rubber cracking + slight steering deviation | Replace within 7 days |
Low | Slight tread wear + occasional noise | Inspect within 30 days |
scientific purchase and replacement: 5 steps to avoid the pit strategy
1).How to Buy High-Quality Control Arm Bushings: The Gold Standard
Step 1: Accurate matching
Operation guide: Provide OE number, VIN code or original bushing sample to ensure that the hole position, size and installation mode are fully suitable
Points of pit avoidance: Avoid purchasing only based on model year, fine-tune suspension structure of some models after replacement (such as the difference between 2020 model and 2023 model)
Step 2: Material adaptation
Material selection for extreme environments:
✅ -60℃ high cold area: choose triple temperature domain compensation technology bushing
✅ +160℃ desert high temperature: silicone alloy formula, anti-aging increased by 50%.
Modification requirements: Preferred polyurethane bushings for track/off-road scenarios (80% increase in compressive strength)
Step 3: Certification assurance
Required qualification: IATF 16949 certified factory (non-trader), test report should contain salt spray test (≥1000 hours), dynamic fatigue test (≥3 million times).
Pit avoidance points: Beware of “copycat certificate”, verify the authenticity of the factory certification number via official website.
Step 4: Standardization of the replacement process
Essential tools: hydraulic press (pressure range 5-20 tons), laser locator (accuracy ±0.1mm), torque wrench (tolerance ±3N·m).
Operation specification:
✅ Removal of old bushing: flame cutting is strictly prohibited to avoid thermal deformation of the frame.
✅ New bushing pressing: apply special grease, vertical pressure to prevent deviation.
Step 5: Verify after replacement
Four-wheel positioning calibration: anterior beam angle and camber angle are adjusted to the original factory parameters (tolerance ±0.15mm).
Dynamic performance test:
✅ Road test: 60km/h emergency braking, detection of body posture stability.
✅ Equipment verification: chassis vibration spectrum analysis of shock absorption efficiency (must reach 85% or more).
2).The whole process of replacement
Pre-diagnosis: measure shape variables and make replacement plans.
Professional tools: hydraulic press + customized fixture to avoid frame deformation.
Torque calibration: installation tolerance ±3N·m to ensure stability.
Dynamic test: spectral analysis to verify the shock absorption effect.
Intelligent monitoring: equipped with wireless sensors, real-time monitoring of life.
FAQ
Incision observation: the inner fiber layer is uniform without bubbles, the rubber elastic recovery is fast, and the metal shell is not rusted.
-60℃ environment: triple temperature domain compensation technology is selected; +180℃ high temperature: silicone alloy formula, heat aging resistance increased by 50%.
The minimum order for conventional models is 500 sets, and small batch trial orders (minimum 50 sets) are supported. Demand assessment is required for customized models.
Ordinary rubber bushings are about 50,000-80,000 km, and polyurethane bushings can reach 100,000 km +. Regular cleaning of oil and avoiding overload can extend life by 30%.
Must! Replacing the bushings will change the suspension geometry parameters, which should be calibrated to tolerance ±0.15mm with a laser locator.
Oil leakage needs to be replaced immediately, hydraulic oil loss will lead to shock absorption function failure. Repair is not recommended because of irreversible damage to the sealing structure.
Slightly REDUCED COMFORT (15% increase in vibration transmission), but 30% increase in handling, recommended for track or modified cars.
Conventional model 7-15 days (air freight), support DDP/DAP logistics, provide full customs declaration documents.
Material cost (PU is 40% more expensive than rubber), process accuracy (±0.01mm tolerance requirements), certification standards (IATF factory premium 10%-15%).
Our control arm bushings come with a 2-year / 50,000 kilometers warranty, covering material defects and production issues. Enjoy free technical consultation and seamless replacement support for OEM control arm bushings.
Listen to our clients how to saying about us
You will quickly understand our capabilities from our clients’ reviews.
The control arm bushing of MIVO is very perfect, reducing vehicle vibration and improving driving experience. I have no concerns about the quality of their products.
MIVO control arm bushings are beneficial to our customers in our auto dealer service centers. They improve alignment and control. MIVO’s reliable quality makes them a popular choice, especially as their tech support is helpful.
I decided to modify my car’s suspension using MIVO’s control arm bushing since I’m a do-it-yourself enthusiast. Installing them is simple. The installation process is made simple by MIVO’s easy-to-follow instructions. I advise you to purchase from them.