Front Control Arm Bushing
End chassis abnormal noise and positioning misalignment caused by Front Control Arm Bushing failure
✅ 20 years of automotive grade rubber formula + military grade production process.
✅ IATF 16949 certified factory direct supply, 72 hours sample urgent delivery.
✅ Suspension system life increased by 40%.
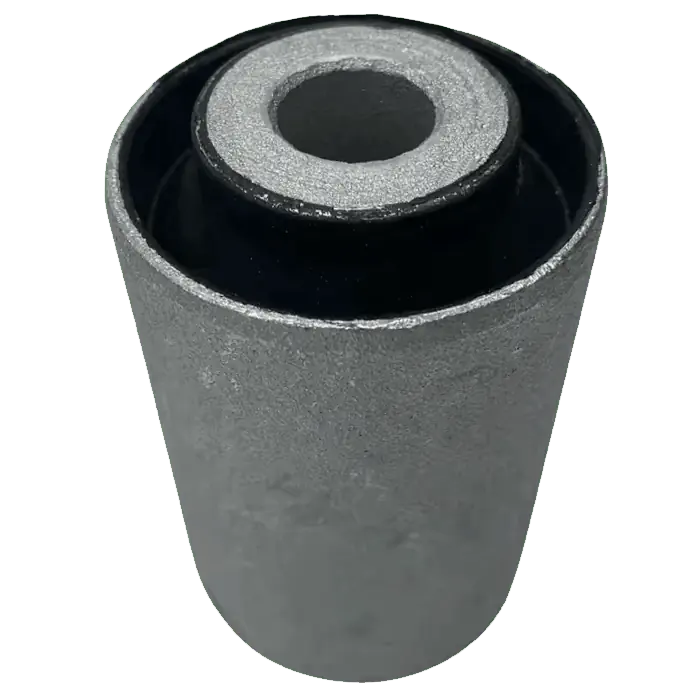
Front Control Arm Bushing : Technical Guide & OEM Manufacturing Solutions | MIVO
As the core shock absorbing component of suspension system, Front Control Arm Bushing directly affects vehicle handling and NVH performance by absorbing road vibration and maintaining wheel positioning parameters.
Reply within 2-8 hours
Via E-mail
MIVO sales and technical teams provide service 24/7
1. What Makes Quality Front Control Arm Bushings?
We deconstruct its key technical elements from the perspective of materials engineers:
1.1 Material Innovation matrix
High damping rubber formula: self-developed HNBR+ carbon fiber composite material with fatigue life exceeding 5 million cycles (SAE J2562 standard)
Temperature adaptability map: dynamic stiffness fluctuation < 15% under -40℃~130℃ (third-party SGS test report is available upon request)
Environmental protection upgrade scheme: Phthalate-free formula meets the EU REACH regulation and is suitable for lightweight requirements of new energy models
1.2 Evolution of structural design
Dual-liquid injection molding process to achieve metal-rubber molecular bonding, peel strength ≥8MPa (60% higher than traditional vulcanization process)
The stress distribution was optimized by three-dimensional finite element analysis (FEA), and the axial offset was controlled within ±0.15mm
Anti-fretting wear patented design, to solve the bushings abnormal noise industry pain points
1.3 Performance verification system
Bench test: MTS 329 shaking table simulates 250 000 km equivalent road test
Real vehicle verification: Jointly developed verification agreements with Oems such as Changan and Geely
Data visualization: Provides reports on 20+ key parameters such as dynamic stiffness-frequency curves and creep recovery rates
2. Why Choose Us as Your Bushing Manufacturer?
2.1 Manufacturing strength in vertical field
Capacity guarantee: fully automated production line to achieve a daily output of 15,000 standard products, emergency orders 72 hours response
Process combination: master three core processes of rubber injection molding/hydraulic vulcanization/polyurethane pouring
Quality control traceability: laser marking for each batch, supporting blockchain traceability of production data
2.2 Customized development roadmap
- Customer demand input
- ↓
- CAE simulation (3 working days)
- ↓
- mold development (10-15 days)
- ↓
- Small batch trial production (50 pieces minimum)
- ↓
- OEM standard certification
- ↓
- mass production delivery
Note: Provide free design optimization consulting services to reduce customer R&D costs
2.3 Quantitative value model
Through process innovation to help customers achieve:
Assembly efficiency improvement: preinstalled bolt design reduces production line man-hours by 23%
After-sales cost reduction: 5 years / 200,000 km warranty commitment
Supply chain optimization: China/Vietnam dual production base supports the optimal tariff scheme
3. Industry Pain Point Solution Library
3.1 Diagnosis of common failure modes
Failure Phenomenon | Root Cause | Our Solution |
---|---|---|
Early bushing cracking | Insufficient rubber vulcanization | Adopt X-ray online detection system |
Metal part corrosion | Electrophoresis process defects | Zinc-nickel alloy + nano-coating treatment |
Abnormal noise | Clearance increase due to fretting wear | Patented wave-shaped contact surface design |
3.2 Technical Memorandum of selection
Passenger car: A radial gradient stiffness design with a hardness of 65±3 Shore A is preferred
Commercial vehicles: Polyurethane composite solutions with limit structures are recommended
Retrofit market: Offers adjustable preload competitive bushing
FAQ
▶ Provide 3D drawings/sample car reverse engineering services, the database has covered 98% of the mainstream model parameters, support free fit simulation test.
▶ Can issue ISO 9001/IATF 16949 system documents, support oems PPAP submission, and provide German TUV material certification report.
▶ From 100 pieces for trial order, delivery in 14 days for regular products, 7 days for expedited channel (50% freight subsidized by air), support for VMI inventory hosting.
▶ Adopt aerospace-grade silica gel base material + dynamic temperature compensation structure, and the stiffness change rate is less than 8% under the environment of -50℃~150℃ (attached with MIL-STD-810 test video of US military standard).
▶ Provide free bench comparison data with common brands (Lemforder, Meyle, etc.), including 6 key indicators such as dynamic stiffness and fatigue life.
▶ Only need to provide: ① load spectrum of working conditions ② installation space dimensions ③ target life cycle, and the rest CAE simulation/mold design will be completed by us.
▶ 15 minutes response →48 hours root cause analysis → free replenishment in advance payment, support third-party institutions to review disputes.
▶ Develop conductive rubber bushing (resistance < 5Ω) to eliminate high-frequency current corrosion of electric vehicles, which has been applied to BYD, NIO and other models.
▶ Vietnamese factories can enjoy the preferential treatment of EU 0 tariff/ASEAN Free Trade Area, and Chinese factories can apply the RCEP agreement, and the optimal solution of intelligent deployment of dual origin.
▶ Open 360°VR online factory inspection, and enjoy free airport pick-up for offline reservation + accompanied by Chinese, English, German and Japanese technical team. Exclusive annual discount will be given upon passing the inspection.
Listen to our clients how to saying about us
You will quickly understand our capabilities from our clients’ reviews.
We can no longer find the accessories related to our old car. MIVO engineers made samples and sent them to us in just 3 days, even considering the compensation of ± 1.5mm caused by process deviation, and quickly reached an agreement with us p>
I have discovered many suppliers in China, and MIVO always considers them very thoughtfully. It has been a pleasant cooperation and I trust them very much p>
MIVO’s products are really good. They have customized multiple solutions for me, and they have increased the suspension system life by 40% Perfectly solved my problem p>