Rear Control Arm Bushing
Customized Rear Control Arm Bushing from ISO certified factory.
Solve the problem of abnormal noise and loose suspension
15 days fast delivery, 3 times longer life silent solution.
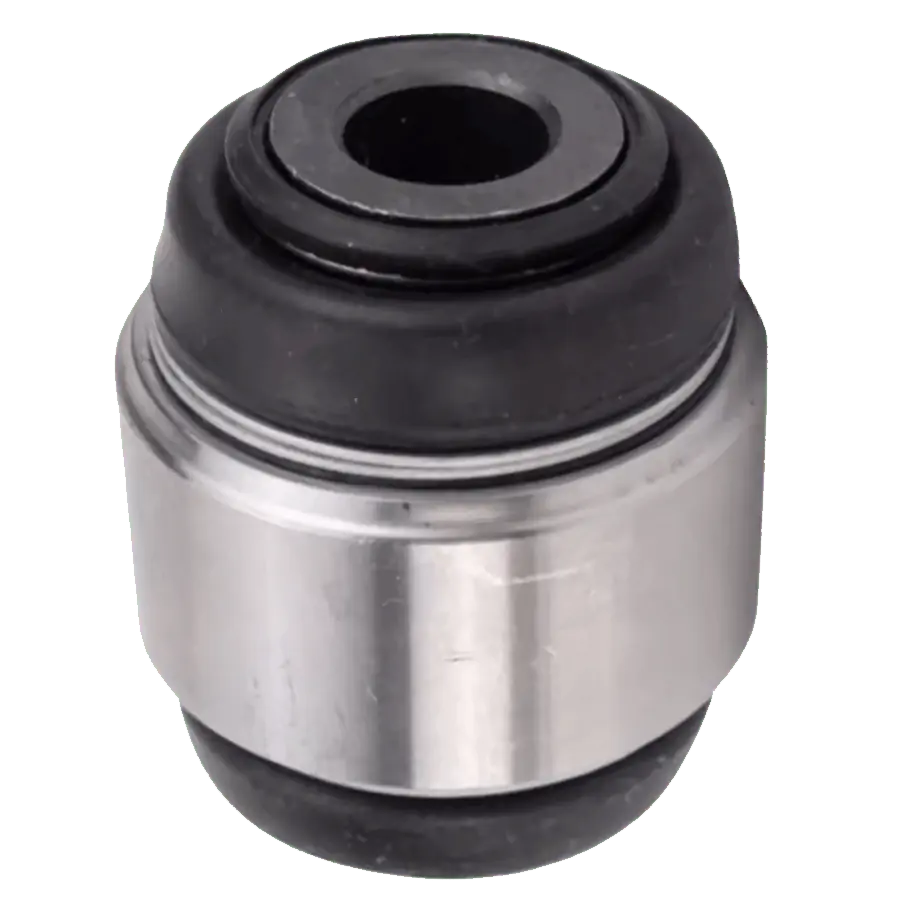
The Ultimate Guide to the Rear Control Arm Bushing
Reply within 2-8 hours
Via E-mail
MIVO sales and technical teams provide service 24/7
- Rear Control Arm Bushing: The core component of suspension can not be ignored
- Why choose our Rear Control Arm Bushing?
- Typical application scenarios of Rear Control Arm Bushing
- In-depth analysis of common problems of customers
- Commitment to sustainable manufacturing
- Make the cooperation process transparent
1. Rear Control Arm Bushing: The core component of suspension can not be ignored
Rear control arm bushing, as a key buffer component connecting the vehicle control arm and the frame, directly affects:
✅ Damping performance of suspension system (35% reduction in road impact)
✅ Tire grip stability (20% reduction in abnormal wear)
✅ Cockpit noise control (NVH value optimized 12-18dB)
✅ Steering accuracy and safety redundancy
According to the needs of different models, we provide three mainstream process solutions:
Rubber-metal composite type: imported from Germany EPDM rubber + laser welding steel sleeve, suitable for -40℃~120℃ extreme environment
Polyurethane high performance type: adjustable shore hardness 85A-95A, tear strength up to 45MPa
Hydraulic damping type: built-in silicone oil buffer layer, effectively absorb high frequency vibration
2. Why choose our Rear Control Arm Bushing?
2.1 Manufacturing advantages of the whole industry chain
Vertical integration from raw material synthesis to finished product packaging:
Rubber mixing workshop: equipped with mixer to achieve ±0.5% material ratio accuracy
Curing production line: 32 sets of 2800T hydraulic press to ensure curing temperature ±1℃ control
Quality Inspection center: 3D profiler/fatigue tester simulates 500,000 dynamic loads
2.2 Strict quality control system
Each batch of Rear control arm bushing should pass 6 key tests:
Test Items | Standards | Qualified Threshold |
---|---|---|
Radial Stiffness | DIN 53504 | Deviation ≤8% |
Dynamic Fatigue | SAE J2562 | ≥500,000 cycles |
Weather Resistance | ASTM D573 | No cracking at 70℃×1008h |
Salt Spray Corrosion | ISO 9227 | Rust area<3% after 720h |
Material Composition Analysis | ASTM D297 | Rubber purity≥98% / Metal sulfur content≤0.02% |
Dimension Accuracy | ISO 3302 | Critical aperture ±0.15mm / Concentricity≤0.3mm |
2.3 Quick response engineering services
DFM analysis of drawings should be completed within 3 working days
Delivery of the first sample within 15 days (expedited by air)
Flexible MOQ policy: the minimum order for conventional models is 50 pieces, and mixed models are supported
3. Typical application scenarios of Rear Control Arm Bushing
Our products have been successfully applied to:
🔧 New energy vehicles: Solve the suspension load problem caused by battery pack weight gain (verified Model Y adaptation scheme)
🔧 Commercial fleet: Extend the maintenance period of heavy duty trucks to 150,000 km
🔧 Retrofit Market: Development of competitive grade polyurethane bushings with optional hardness and color customization
🔧 After-sales replacement parts: 100% match the original factory installation hole position, with 3D installation guidance video
4. In-depth analysis of common problems of customers
Q1: How to determine whether the Rear control arm bushing needs to be replaced?
Testing is recommended when the following symptoms occur:
“Creak” abnormal sound over the speed reducer (caused by aging and cracking of rubber)
Virtual position of steering wheel increases (bushing deformation affects geometric positioning)
Irregular tire wear (suspension dynamic parameter misalignment)
Q2: How to choose Rear control arm bushing with different materials?
✓ Daily scooter: rubber model is preferred to balance comfort and cost
✓ Performance modification car: polyurethane model is recommended to improve handling response
✓ High cold/high heat area: fluorine rubber formula is recommended
Q3: Is it necessary to do four-wheel positioning after installation?
Must be implemented! Replacing the Rear control arm bushing will change the position of the hard point of the suspension. We suggest:
Use a laser locator to calibrate the backdip Angle of the kingpin
Tighten the bolt to 120N·m torque after road test
5. Commitment to sustainable manufacturing
As a green factory benchmark, we have passed:
♻️ 100% recycling and recycling of rubber waste (cooperation with Chinese Academy of Sciences to develop recycled rubber technology)
♻️ Zero discharge system for production wastewater (reverse osmosis treatment reaches GB/T 31962 standard)
♻️ Carbon footprint traceability system (production energy consumption data can be queried for each product)
6. Make the cooperation process transparent
Requirements communication: Submit model/material/certification requirements
Solution confirmation: Obtain 3D drawings and technical agreement
Sample verification: provide 5 test loading parts free of charge
Mass production delivery: real-time feedback of production progress from exclusive documentary staff
After-sales service: 12 months warranty period + lifelong technical support
Listen to our clients how to saying about us
You will quickly understand our capabilities from our clients’ reviews.
“Rear bushings arrived pre-lubricated and with dowel pins – reduced installation time by 30%. 12,000 miles on a county snowplow with no cracks. Bushings fit perfectly even with the tool we borrowed.”
We ran out of stock, contacted MIVO, they immediately started production and it was delivered to me in 72 hours.
“Over 500 bushings were quality inspected to ensure tolerances. Their bushings meet specifications, and material certificates are provided for each batch, which can also be submitted online.”