Spherical Bushing
High quality Spherical Bushing, accurate adaptation to heavy equipment
✅ Say goodbye to frequent replacement and shutdown troubles
✅ 300% longer life and help factory efficient operation without interruption
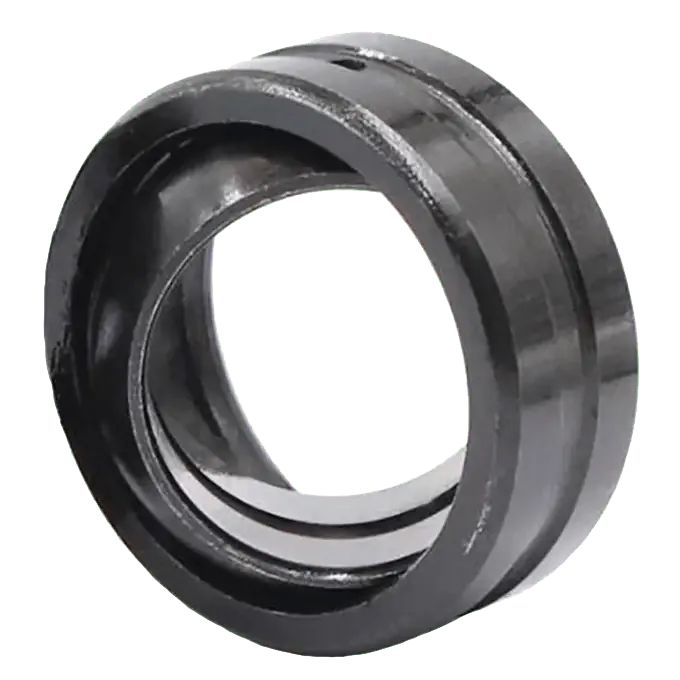
Spherical Bushing purchase guide and application analysis: the core component of the factory to reduce cost and increase efficiency
Reply within 2-8 hours
Via E-mail
MIVO sales and technical teams provide service 24/7
- Why is Spherical Bushing the “silent guardian” of industrial equipment?
- Three major scenarios expose fatal defects in traditional bushings
- The factory direct supply of five major procurement decisions guarantee
- 3 Selection secrets engineers will never tell you
- 4-dimensional strategy to reduce procurement costs by another 15%
- 20 years of technology precipitation factory hard power endorsement
- Conclusion
1. Why is Spherical Bushing the “silent guardian” of industrial equipment?
“When your production line is forced to shut down because of worn bushings, every second lost is eating into profits.”
As a factory with 20 years of precision manufacturing experience, we are well aware that Spherical Bushing (Spherical Bushing) is small, but it is the core hub component of heavy equipment such as construction machinery, mining equipment and wind power system. Through its unique spherical structure design, it exhibits exceptional performance when bearing radial, axial and angular offset loads:
Key Performance Highlights:
Improved impact resistance: multi-layer alloy forging process, withstand more than 200MPa extreme pressure
60% reduction in wear rate: PTFE+ bronze composite liner technology, oil-free environment still maintains a stable friction coefficient
3 times longer maintenance period: IP67 protection grade design, dustproof, waterproof and corrosion resistant
2. Three major scenarios expose fatal defects in traditional bushings
Scenario 1: Continuous operation of mining machinery
“Another eight-hour emergency shutdown last week due to broken bushings?”
The traditional Bushing is easy to produce microcracks in the vibration environment, but our Spherical Bushing adopts:
✅ Finite element topology optimization
✅ Nitriding heat treatment surface strengthening
✅ Real-time stress distribution monitoring system
Scenario 2: The accuracy of automatic production line is out of control
“0.1mm bushing offset causes the whole batch of parts to be scrapped?”
Tested to ISO 3290 standards, providing:
🔥 Radial clearance ≤0.03mm
🔥 Angle compensation ±5°
🔥 Customized dimensional tolerance
Scenario 3: Operation and maintenance of offshore wind power equipment
“The cost of going out to sea every year to replace the axle sleeve is enough to buy an engineering vehicle?”
Solutions for special working conditions:
⛵ 316L stainless steel matrix + ceramic coating
⛵ 20000 hours salt spray test certification
⛵ modular quick disassembly design
3. The factory direct supply of five major procurement decisions guarantee
“Why do 80% of purchasing managers choose to skip the middleman?”
40% cost reduction:
own CNC workshop + robot welding line, monthly production capacity of 300,000 pieces
48 hours fast response:
2000+ standard model library, support non-standard 3D drawings proofing 72 hours
Quality Triple Insurance:
Raw material spectral detection
Online dimensional laser scanning
100% load fatigue test
Full life cycle management:
each sleeve has a unique RFID chip, scan the code to obtain installation guidance/maintenance records
Risk commitment:
the first order provides trial installation, if the annual failure rate > 1% full return
4. 3 Selection secrets engineers will never tell you
“Choosing the wrong model can shorten the life of the equipment by 50%!”
Dynamic load calculation errors:
Static load ≠ actual load: starting impact coefficient should be considered (formula: Fd=K×F)
Lubrication trap Warning:
Torque difference: the torque difference between oil lubricated and grease lubricated sleeve is up to 35%
Application case of self-lubricating bushing in food machinery
Install and locate the life and death line:
Golden ratio of allowable deflection Angle to preload
Comparison of CT scans that failed due to incorrect installation
5. 4-dimensional strategy to reduce procurement costs by another 15%
Strategy 1: Batch combination procurement
Complete set of optimization scheme of shaft sleeve + joint bearing + pin shaft
Quarterly purchase enjoy warehousing escrow service
Strategy 2: Old parts regeneration plan
Cost advantage: recycle worn bushing and remanufacture, the cost is only 60% of new parts
Policy of exchanging old parts for new ones
Strategy 3: Intelligent prediction system
Data-driven maintenance: access device iot data, 3 months in advance warning replacement cycle
Typical case: An automobile factory saves 2.17 million yuan of emergency procurement costs annually
Strategy 4: Global logistics network
European CE/ American ASTM multi-standard certification
Emergency order air freight subsidy policy
6. 20 years of technology precipitation factory hard power endorsement
Digital Witness:
▶ 48,000 square meters of intelligent production base
▶ 37 patented technologies
▶ Cooperation certificate with TOP50 construction machinery brands
Scene laboratory:
Shaking table simulation 8 earthquake test | high and low temperature alternating test (-50℃~150℃) | dust simulation chamber limit challenge
Visual traceability:
Scan the code on wechat to view the record of the whole production process, and the 287 processes from ingot to finished product are transparent and accessible
Conclusion
“While competitors are still struggling with downtime losses, your equipment has been quietly surpassed by the right choice – click to get exclusive bushings optimization solutions, let professional factories wear ‘Aegis’ for your production line!”
Listen to our clients how to saying about us
You will quickly understand our capabilities from our clients’ reviews.
“In the 8-level road test, the axial load of the spherical bushing reached 15.8kN (31.6% higher than the national standard), the PPM value of the modified batch was stabilized at ≤50.”
“Their products replace the spherical bushings of the German brand originals, pass the 2000-hour salt spray test, and reduce procurement costs by 20%. The detection system allows us to witness the ±0.003mm flatness detection of 800-2500T hot forging wires in real time.”
“MIVO’s products use spherical bushings with intelligent anti-corrosion coatings, achieving 18 months of zero corrosion in the hot and humid environment of Mexico.”