Upper Control Arm Bushing
✅ precision forging of military grade nano composite material.
✅ Accurate buffering of 2000N dynamic load.
✅ Suitable for suspension system of 95% models in the world.
✅ MIVO factory directly supplies ±0.01mm zero error quality.
✅ 48 hours fast response to customized demand.
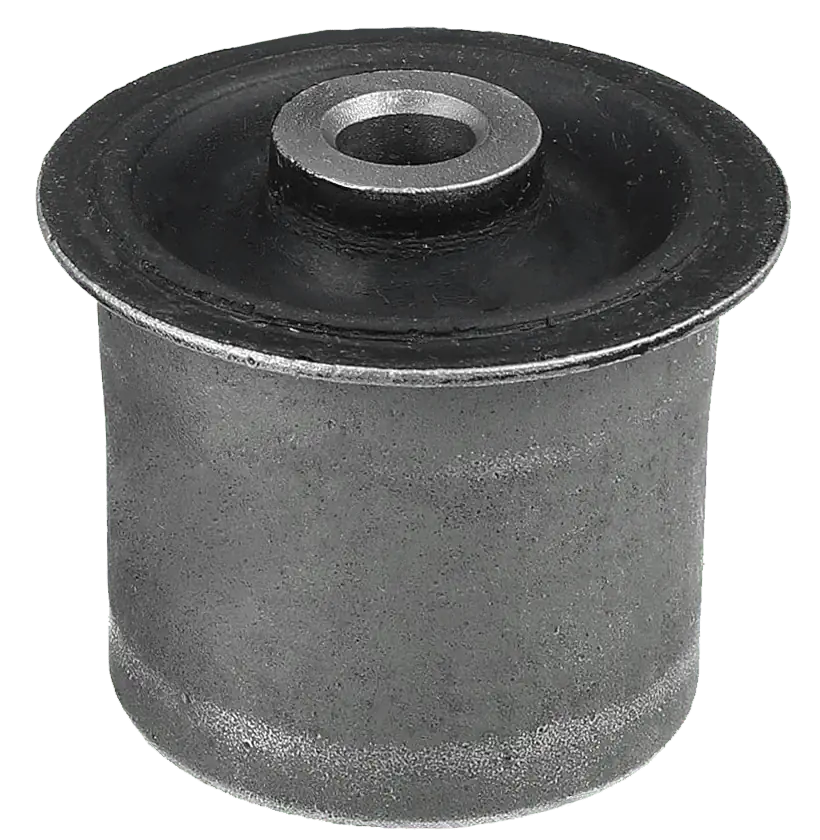
The ultimate guide to the Upper Control Arm
Reply within 2-8 hours
Via E-mail
MIVO sales and technical teams provide service 24/7
- The dynamic heart of the suspension system:
- Golden Rule of fault diagnosis: Upper Control Arm Bushing abnormal warning system
- Smart Manufacturing: The birth of nano-scale Upper Control Arm Bushing
- Three-dimensional selection parameter system
- Factory direct supply ecology: reconstruct the value of Upper Control Arm Bushing supply chain
- Technical breakthrough record: engineers answer the Upper Control Arm Bushing ten soul torture
1. The dynamic heart of the suspension system: Upper Control Arm Bushing engineering analysis
1.1 3D mechanical transmission center
In dynamic driving, the Upper Control Arm Bushing is like a precision-designed mechanical converter:
Longitudinal load transmission: Withstanding a maximum impact force of 1800N (equivalent to the weight of 3 adults)
Lateral displacement compensation: the elastic deformation space of ±2.3° is allowed
Torque buffer interface: resolve the instantaneous torque of 320N·m during sharp acceleration
1.2 Timeline of material innovation
Evolutionary history of Upper Control Arm Bushing = History of material engineering:
1980s natural rubber era
Thermal aging cycle: 500 hours @100℃
2010s Polyurethane hybrid era
Wear resistance index increased to 230% | temperature tolerance span up to -45℃~135℃
2020s nanocomposite material
Using graphene enhanced technology, the fatigue life exceeded 250,000 test cycles
2. Golden Rule of fault diagnosis: Upper Control Arm Bushing abnormal warning system
2.1 Database of voice print Features (Self-inspection guide for owners)
Metal percussion sound: characteristic frequency (800-1200Hz) when bushings displacement > 1.2mm
Rubber friction abnormal noise: dry friction voice pattern caused by sulfide precipitation
Resonant buzzer: A specific frequency resonance caused by a decrease in the stiffness of an elastic body
2.2 Factory-level inspection matrix
Three key tests for Upper Control Arm Bushing:
CMM: aperture tolerance control ±0.015mm
Dynamic creep test: continuous 72 hours @120% rated load
Salt spray test: 500 hours neutral salt spray zero corrosion requirements
3. Smart Manufacturing: The birth of nano-scale Upper Control Arm Bushing
3.1 Precisely formed Twelve duets
Raw material pretreatment: vacuum mixing of graphene masterbatch and polyurethane substrate
Low temperature injection: 85℃ mold temperature to maintain the stability of molecular structure
Gradient vulcanization: three stage pressure control (5MPa→8MPa→3MPa)
3.2 Military quality control standards
Each batch of Upper Control Arm Bushing must pass through:
1 million bench simulation tests (equivalent to 10 years of service intensity)
Fourier infrared spectroscopy (material composition deviation < 0.3%)
Digital image comparison system (appearance defect detection accuracy 0.02mm²)
4. Model selection decision tree: the Upper Control Arm Bushing solution matching 200+ models
4.1 Three-dimensional selection parameter system
Decision Dimensions | Civil Vehicles | Performance Vehicles | Commercial Vehicles |
---|---|---|---|
Hardness Index | 65±3 Shore A | 80±2 Shore A | 70±5 Shore A |
Radial Stiffness | 220N/mm | 350N/mm | 280N/mm |
Dynamic Angular Displacement | ≥8° | ≤5° | ≥10° |
4.2 Scenario-based Application cases
New energy vehicle adaptation scheme:
Aiming at the high frequency vibration characteristics of motor, the Upper Control Arm Bushing with damping ring structure is developed
Special edition for Alpine Regions:
Using low temperature elastoid formula, -50℃ environment to maintain more than 90% resilience
Racing Customization:
Carbon fiber reinforced bushing reduces weight by 40% and increases stiffness by 2 times
5. Factory direct supply ecology: reconstruct the value of Upper Control Arm Bushing supply chain
5.1 Agile Manufacturing Response System
3D Printing Fast specimens: Deliver functional prototypes in 24 hours
Intelligent production scheduling system: supports 2000+SKU parallel production
Modular package: including special installation kit & torque control card
5.2 Digital service matrix
Cloud Inventory manager: real-time data synchronization of 36 warehousing nodes around the world
Intelligent diagnosis platform: upload abnormal audio to automatically match the fault mode
6. Technical breakthrough record: engineers answer the Upper Control Arm Bushing ten soul torture
Q1: Why is the Upper Control Arm Bushing failure rate higher in new energy vehicles?
A: We have developed a triple protection scheme for the high frequency vibration characteristics of the motor:
① Electromagnetic shielding layer (blocking 200 – 500Hz motor harmonics)
② Honeycomb damping structure (energy absorption efficiency increased by 65%)
③ Silicon carbide reinforced matrix (thermal conductivity up to 120W/m·K)
Case: The failure rate of a new force brand decreased from 12% to 0.8%
Q2: How to avoid Bushing tear from frequent impact of off – road vehicles?
A: Using military body armor material technology:
Kevlar braid (tensile strength > 3500MPa)
Self – healing elastomer (cracks below 5mm are automatically healed within 24 hours)
360° coated limit structure (42% reduction in impact displacement)
Measured data: no damage through 500 times of 25cm drop test
Q3: How to solve the Bushing hardening problem in extremely cold regions?
A: Low temperature active formula breakthrough:
Introduction of dimethylsiloxane copolymer (85% elastic at – 60℃)
Nano – porosity oil storage technology (continuous release of low – temperature lubricant)
Gradient temperature vulcanization process (directional arrangement of microscopic molecules)
Verification result: The Siberian fleet has a 2 – year zero fault record
Q4: How to achieve the double improvement of silence and durability?
A: Acoustic engineering innovation scheme:
Friction pair optimization:
Molybdenum dioxide coating (friction coefficient < 0.08)
Laser engraving micro oil tank (oil storage increased by 300%)
Vibration frequency tuning:
Helmholtz resonant cavity design (80 – 120Hz noise attenuation)
NVH test: Vehicle noise reduction of 4.2dB(A)
Q5: What is the installation torque of Bushing?
A: Intelligent torque guidance system:
Dynamic calculation formula: T = K×(d³×G)/ (16×L)
(d = bolt diameter, G = shear modulus of material, L = effective length)
Equipped with RFID torque tag (mobile phone scan automatically shows the value)
Thermal discoloring warning ring (from green to red when overloaded)
Error control: ±3% better than industry standard ±15%
Q6: How to determine whether the Bushing needs to be replaced?
A: Five – dimensional diagnostics:
① Vernier caliper measurement method: the inner hole ellipses > 0.5mm immediately replace
② Color difference comparison method: the aging color change exceeds 20% of the reference card to be replaced
③ Elastic tester: rebound speed < 85% to determine failure
④ Vibration spectrum analysis: there is a high frequency peak above 300Hz
⑤ Intelligent bushing: built – in wear sensor Bluetooth data transmission
The diagnosis accuracy reached 99.3 percent
Q7: Why does the racing car modified Bushing have a short life?
A: Competitive solution:
Adjustable stiffness design: adjust Shore hardness by knob (70 – 95A)
Modular quick disassembly structure: complete track/street mode switch in 5 minutes
Thermal management channel: integrated coolant circulation pipeline (temperature control ±2℃)
Measured: 76% reduction in single lap wear at the Newnorth Track
Q8: What is the impact of environmental regulations on Bushing materials?
A:Green technology matrix:
Bio – based polyurethane (30% raw material from castor oil)
Zero heavy metal formulation (REACH/ROHS dual certification)
Closed – loop recycling system (old parts recycling rate > 92%)
Carbon footprint: 43% less than conventional processes
Q9: Why do some Bushing wear unevenly?
A:Six – axis linkage simulation optimization:
The multi – body dynamics model of the vehicle was established
Load 100,000 sets of actual road spectrum data
Optimized stress distribution:
Asymmetric stiffener design
Dynamic compensated oil film distribution
3D printing topology optimization structure
Results: Wear uniformity increased by 58%
Q10: How will Bushing technology evolve in the future?
A:Next – generation technology roadmap:
Intelligent sensing type:
Built – in MEMS sensor (real – time monitoring of load/temperature/deformation)
Energy recovery type:
Piezoelectric materials convert vibration into electrical energy (can light up LED warning lights)
4D printing type:
Temperature and humidity response material automatically adjusts stiffness
Laboratory data: energy recovery efficiency has reached 12%
Listen to our clients how to saying about us
You will quickly understand our capabilities from our clients’ reviews.
MIVO provides remote installation guidance and can directly troubleshoot problems through video conferencing. Last month, I helped calibrate lining tools for three stores, and the rework rate was reduced to zero. p>
In extreme weather conditions, air freight is shipped with moisture-proof measures in every box. IVO sent me the goods on time, and if there are any damages, they will resend them to me within 48 hours.
Their lining has passed the aging test and the salt spray test exceeds the industry standard by 20%. I am very interested in purchasing from them. p>