Rear Control Arm
MIVO manufacturers supply Rear Control Arm for you
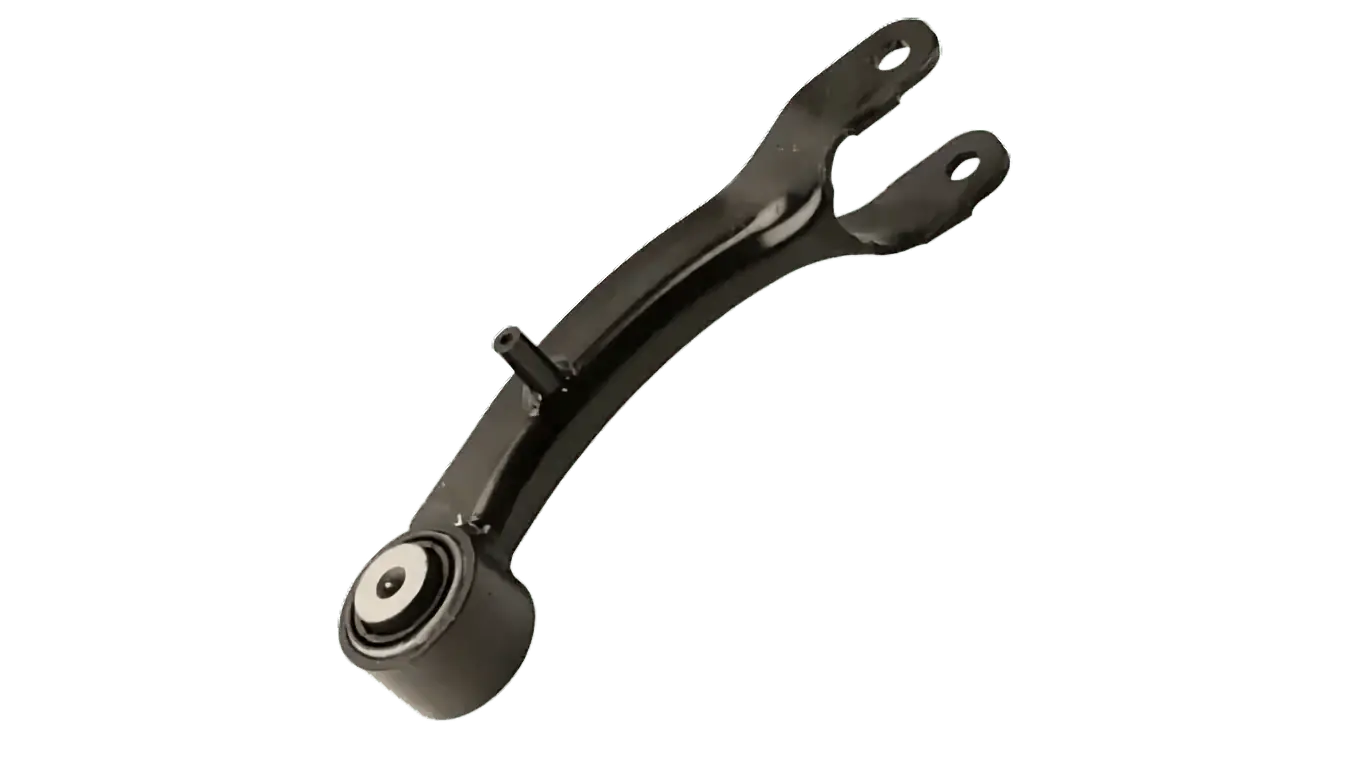
The ultimate Guide to Rear Control Arm: Design principles, manufacturing processes and Global OEM plant selection strategies
Deeply analyze the core function, material science and production technology of automobile rear control arm. As an OEM manufacturer of automotive suspension systems with 30 years of experience, this paper reveals 12 key technical indicators and golden rules for factory selection of high-end control arms.
Reply within 2-8 hours
Via E-mail
MIVO sales and technical teams provide service 24/7
- Technical anatomy of Rear Control Arm: the core mechanical transmitter of automobile chassis
- High-end Rear control arm manufacturing 7 major process breakthrough points
- 6 Election decision matrix that global buyers must see
- Industry pain point solutions: Five technological innovations to cope with extreme working conditions
- Procurement decision support: 3 steps to locate high-quality suppliers
- Why choose us?
1. Technical anatomy of Rear Control Arm: the core mechanical transmitter of automobile chassis
In the dynamic model of automobile suspension system, the Rear Control Arm undertakes three core missions:
Geometric positioning: the wheel alignment control is restricted by hard point connection
Load transfer: Vertical/lateral force transmission to sub-frame (load transfer mechanism)
Vibration isolation: cooperate with bushings to filter road excitation (vibration damping system)
According to the SAE J670 vehicle dynamics standard, modern control arms are designed to meet:
Longitudinal stiffness ≥1800N/mm (steel) / 1200N/mm (aluminum alloy)
Fatigue life >5 million cycles (ASTM E466 standard test)
Weight tolerance ±2% (lightweight design requirements)
2. High-end Rear control arm manufacturing 7 major process breakthrough points
As a global Tier 1 supplier certified with IATF 16949, our plants adopt a modular manufacturing process:
Stage 1: Material engineering innovation
Alloy steel scheme: HC420LA high strength low alloy steel with yield strength up to 420MPa (elongation 18%)
Aluminum alloy solution: A356-T6 casting process, to achieve specific strength of 8.5kN·m/kg
Hybrid material solution: patented technology enables steel and aluminum laser tailor-welded (LWB), reducing weight by 25% and improving stiffness
Stage 2: Precision forming technology
The 5-axis CNC machining center ensures the accuracy of the installation hole position ±0.01mm
Servo hydraulic press to achieve 6000kN stamping molding (tolerance band ±0.15mm)
Robot welding workstation to ensure weld penetration ≥3mm (in accordance with AWS D1.2 standard)
Stage 3: Quality verification system
Three coordinate measuring instrument (CMM) full size inspection
Salt spray test > 720 hours (ISO 9227 standard)
Bench fatigue tests simulate a 10 year service life
Stage 4: Material engineering innovation
Nano-composite coating technology: using PVD physical vapor deposition process, the friction coefficient is reduced by 40% (in line with VDA 270 standard)
Micro-arc oxidation treatment: 20-50μm ceramic layer is formed on the surface of aluminum alloy, and the hardness reaches 1500HV
Cathodic electrophoretic coating: the film thickness is 30±5μm, passing the 3000 hour cycle corrosion test (GM 9540P standard)
Phase 5: Intelligent assembly system
Visual guidance assembly robot: repeated positioning accuracy ±0.05mm
Servo pressing system: pressing force control accuracy ±1%, real-time monitoring of displacement – pressure curve
Intelligent tightening workstation: dynamic torque control based on ISO 5393 standard with 100% data traceability
Phase 6: Digital process control
Process monitoring based on MES system: key parameter CPK≥1.67
Laser 3D scanning inspection: 0.02mm level reverse engineering verification
Big data analysis platform: realize self-optimization of process parameters, and improve the yield to 99.93%
Phase 7: Sustainable manufacturing technologies
Scrap recycling system: metal utilization increased to 92% (ISO 14001 compliant)
Low temperature powder spraying: energy consumption reduced by 35%, VOC emission < 10mg/m³
Water circulation treatment system: achieve zero discharge of industrial wastewater (GB 8978-1996 standard)
3. 6 Election decision matrix that global buyers must see
By analyzing the procurement data of Top 50 customers, we found that quality suppliers need to meet the following requirements:
Evaluation dimension | Industry benchmark value | Our factory’s technical indicators |
---|---|---|
Annual production capacity | 500,000 pieces/year | 3,000,000 pieces/year (flexible production line) |
Development cycle | 12 weeks | 8 weeks (DFM concurrent engineering) |
Cost optimization space | 8-15% | 22% (value engineering analysis) |
Defect rate | 500PPM | 85PPM (Six Sigma control) |
Mold life | 300,000 stamping times | 500,000 stamping times (SKD11 material) |
Delivery on-time rate | 92% | 99.6% (JIT management system) |
4. Industry pain point solutions: Five technological innovations to cope with extreme working conditions
In view of the special needs of new energy vehicles and off-road vehicles, the R&D department of our factory has achieved key breakthroughs:
Electrophoretic coating upgrade: cathode electrophoresis thickness of 35μm+ micro-arc oxidation treatment, corrosion resistance to C4H (ISO 12944)
Intelligent detection system: embedded strain gauge sensor, real-time monitoring of load distribution (data output frequency of 100Hz)
Topology optimization design: multi-objective optimization was achieved through Altair OptiStruct, and the stiffness was increased by 17%
Quick die changing system: die switching time < 15 minutes (industry average 45 minutes)
Carbon footprint management: 42% reduction in lifecycle carbon emissions per product (EPD Environmental Product Statement)
5. Procurement decision support: 3 steps to locate high-quality suppliers
Based on VDA6.3 process audit standards, it is recommended that purchasers implement:
Technical benchmarking: Require suppliers to provide FEA analysis report and bench test data
Process audit: Focus on SPC control chart and MSA measurement system analysis
Supply chain audit: Verify the material proof (MTC) and heat treatment curve of secondary suppliers
6. Why choose us?
Served 12 global OEMs and delivered 20 million zero-defect products in total
24 hours rapid response to engineering changes (ECN)
Support JIS/JIT delivery mode, leading the industry in inventory turnover by 300%
Provide 5-year warranty commitment and lifetime technical support
Listen to our clients how to saying about us
You will quickly understand our capabilities from our clients’ reviews.
“Had a ’09 Silverado come in last week – customer swore he’d installed three rear arms that ‘never sat right’. Slapped on MIVO’s version, eyeballed the alignment specs… dead nuts on. Even the camber bolts didn’t need shims.”
“Salt trucks eat control arms for breakfast. We’ve had MIVO’s rear arms through two Midwest winters – zero rust jacking around the bushings. Last batch outlived our 24-month replacement cycle by eight months. Council thinks I’m a budgeting wizard now.”
“Burned through two ‘performance’ rear arms at last season’s opener – snapped like twigs on hard angle entries. MIVO’s? Let’s just say I’ve been yanking the e-brake harder. The forged eyelet design… yeah, they actually know what side load means.”