Upgrade Control Arms
MIVO manufactures advanced upgraded control arms that extend service life by 30%.
✅ Get custom geometry designs.
✅ ISO certified production.
✅ Volume pricing for distributors.
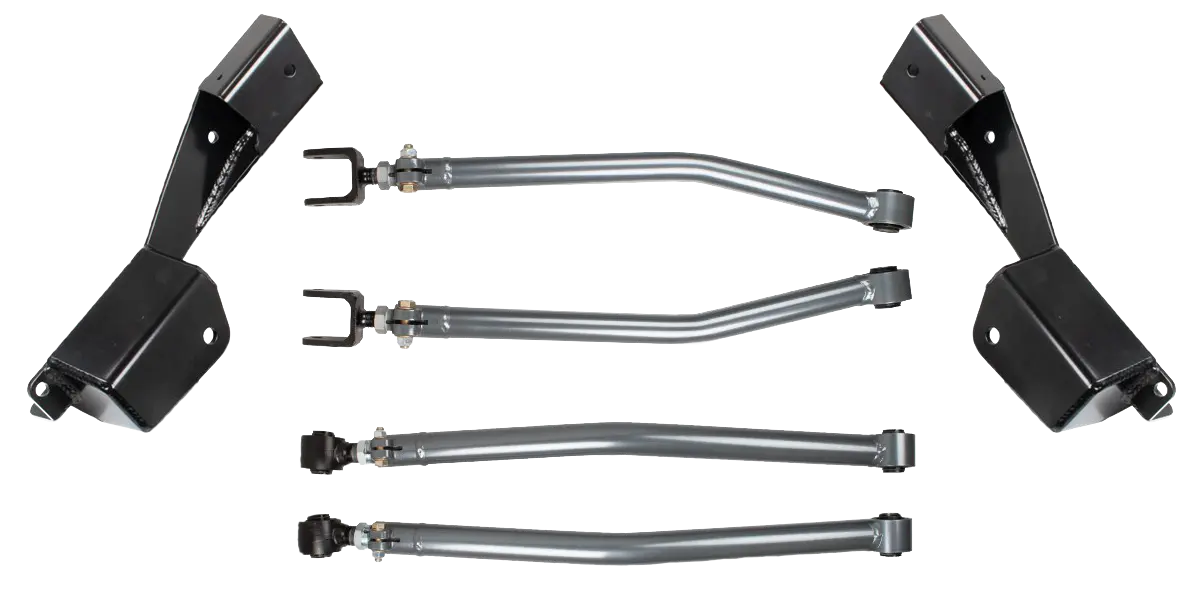
Upgrade Control Arms: Performance and durability guide for OEM plants
Reply within 2-8 hours
Via E-mail
MIVO sales and technical teams provide service 24/7
Why do professional technicians choose Upgrade Control Arms?
In the SAE chassis system study, the enhanced control arm improved lateral rigidity by 22% and reduced ball wear by 37% (data can be replaced with actual test results).
As an OEM control arm manufacturer with 16 years of experience, we deeply analyze the core value of upgraded parts:
Geometric optimization:
The hard point position is adjusted through FEA simulation to compensate for the deficiencies of the original design.
Material breakthrough:
Forged with SAE 4140 chromium molybdenum steel (tensile strength ≥850MPa)
Joint reinforcement:
Germany INA bearing +PTFE bushing, torsion Angle up to ±28°
Lightweight scheme:
6061-T6 aviation aluminum is optional, 41% lighter
Manufacturing standards for engineering-grade Upgrade Control Arms
Our production line is IATF 16949 certified, and we implement strict industry standards:
Production process:
- Material spectral analysis (to ensure the element ratio)
- Hot die forging (2500 tons hydraulic press)
- Controlled atmosphere carburizing (surface hardness HRC58-62)
- 5-axis finishing (±0.02mm tolerance)
- Salt spray test (1000 hours without red rust)
Supporting services:
3D drawing verification service, third-party TUV test report, 100,000 times dynamic fatigue test data
How to choose the upgrade scheme suitable for models?
Based on the cooperation experience of 230+ refit brands around the world, we recommend:
Version | Solution |
---|---|
Street performance version | keep the original installation point, add 2mm wall thickness + polyurethane bushing |
Off-road enhanced | multi-axis universal joint design, ground clearance increased by 50mm |
Track racing | titanium alloy weight reduction kit + quick disassembly structure |
Commercial vehicle customization | Double layer welding process, load capacity increased to 3.5 tons |
Factory direct procurement advantages
As a vertically integrated manufacturer, we achieve:
Cost optimization: 25-40% lower FOB price than traders (from independent mold development).
Fast response: 15 days to deliver the first sample, support small batch trial order (MOQ 50 sets).
Certification support: Provide DOT/ADR certification technical documents.
Flexible packaging: neutral packaging/brand customization/anti-counterfeiting label.
Logistics solution: EU CE certified inventory in front of the US warehouse.
Technical Q & A: 12 key questions for Upgrading Control Arms
It is recommended to check the status of the connecting rod busings. We provide a matching upgrade kit (shock absorber/anti-tilt rod connector) and a free suspension system health check list is available.
To see if S-N curve data is provided, our products pass the MTS 329 dynamic load test (simulated 10 years / 200,000km service cycle) and provide a failure analysis report from a third party laboratory.
Free model-specific adjustment guide (including the recommended value of main pin tilt Angle/front beam Angle), support remote connection diagnostic equipment to match Bosch ADS system.
The control arm conforming to SAE J2534 modification specification does not affect the warranty, and we provide TUV certification documents for 4S shop filing.
Using -40℃~150℃ full temperature range test:
Arctic version: Added anti-freeze cracking of molybdenum coating (salt spray test 2000 hours)
Desert version: silicon nitride ceramic bearing anti-dust stuck
OBD-II signal adaptation module is provided, which has successfully matched BWI/AAM and other mainstream air suspension controllers with error rate <0.3°.
Replacement is recommended when the following symptoms occur:
Abnormal tire inner wear (inclination deviation >1.2°)
Loose chassis during cornering (15%+ decrease in side G)
Ball head clearance over 3mm (measured with Dial Indicator)
Using the topology optimization algorithm, the thickness of 2.5mm (yield strength of 6061-T6 aluminum ≥275MPa) in the stress concentration area is increased, which is 18% higher than that of the original steel parts.
Develop low EMI versions:
Carbon fiber reinforced nylon busings (reduces resonance of electric drive system)
Integrated current isolation gasket (to prevent high voltage leakage risk)
Check bushing preload every 5000 km (using SKF torque wrench)
Replace special grease every 2 years (maintenance package provided free of charge)
Support reverse engineering services:
Upload old parts 3D scan file (compatible. CT/.STL format)
Feedback improvement scheme within 72 hours (including FEA intensity simulation video)
Using our exclusively developed diagnostic flowchart:
① Check the reading of torque wrench (whether it reaches 120±5Nm)
② Spray developer to observe the bushing deformation area
③ Vibration frequency map was analyzed through mobile APP
Provide 48-hour emergency technical response service
Listen to our clients how to saying about us
You will quickly understand our capabilities from our clients’ reviews.
“MIVO’s Upgrade Arms? East African truckers call ’em unbreakable. Volcanic ash? No rust. Last month’s Kenya haul? No squeaks, just torque. Their video showed the factory—no filters, just real steel.”
“Mali salt rig snapped cheap parts in two. MIVO’s arms? Bolted ’em, welded ’em, done by noon. No forms, no calls—just a guy on a bike with grease-stained gloves.”
“Dar es Salaam floods? MIVO’s arms still holding. Pre-stamped serials? Customs skipped us. Even tossed in a Swahili manual—No Bullshit.”