Shock Absorber
MIVO is a leading OEM shock absorber manufacturer, offering full‑range solutions for all vehicle models. Learn what do shock absorbers do, how long they last, and get an instant quote on replacement cost.
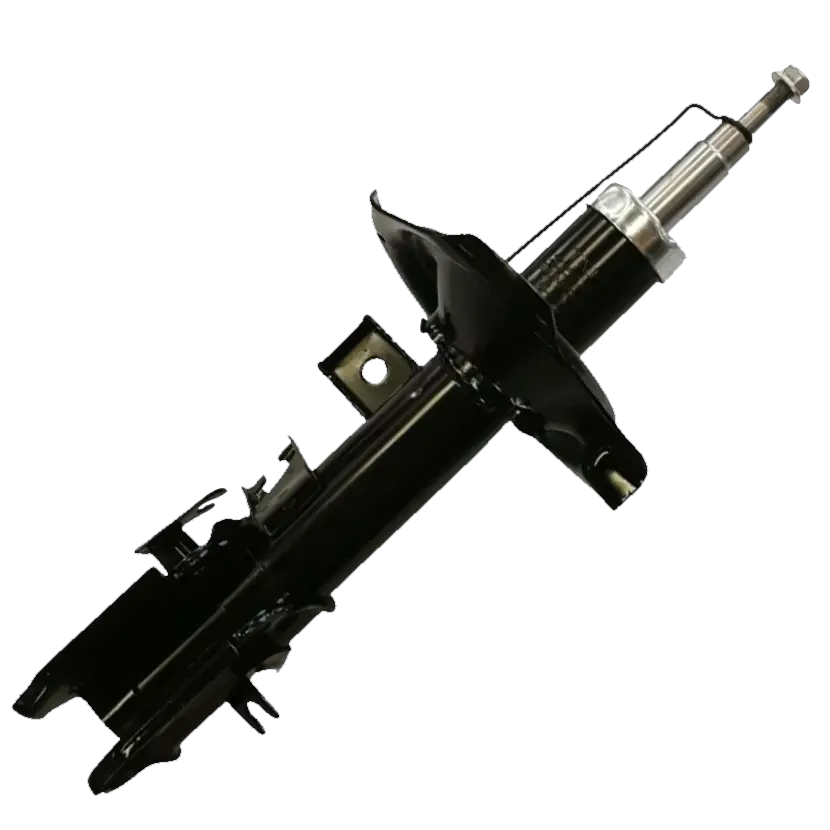
Types of Shock Absorbers: Front vs. Rear
-
Front shock absorber
Front shock absorbers perform a similar function but are located at the front of the vehicle. They manage impacts from uneven surfaces, reduce body roll during turns, and help stabilize steering and braking. Their performance is critical for ride smoothness and handling precision.
-
Rear shock absorber
Rear shock absorbers are components in a vehicle’s suspension system designed to dampen vibrations and impacts from the road, specifically for the rear wheels. They absorb and dissipate energy from bumps, ensuring stability, comfort, and maintaining tire contact with the road for better control.
The world’s leading OEM Shock Absorber manufacturer
OEM Shock Absorbers Manufacturer – 20 Years’ Expertise & Fast Delivery
Certification and capacity guarantee
🛡️International dual certification: ISO 9001 + IATF 16949 system certification, to meet the strict standards of automobile oems.
🏭Large-scale production: monthly production capacity of 500,000 pieces, support large batch order delivery.
🛡️Military technology: hydraulic buffer technology from military projects, resistant to extreme environments (-50℃ to 150℃).
Agile response and supply chain advantages
⚡48 hours fast proofing: special sample production line, shorten the research and development cycle.
⚡7×24 hours FAE support: provide vibration spectrum analysis, remote guidance for installation and commissioning.
💲VMI/JIT supply mode: seamless connection with customer inventory system to reduce supply chain costs.
Different Types of Shock Absorber
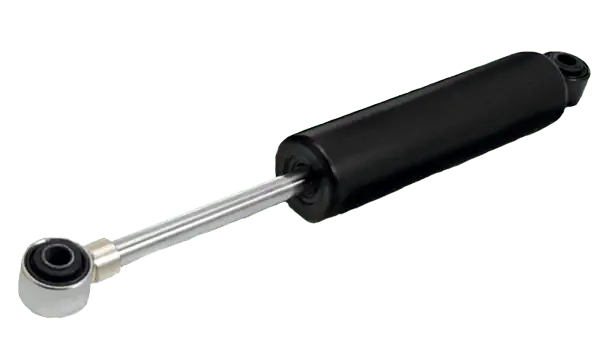
Hydraulic Shock Absorber
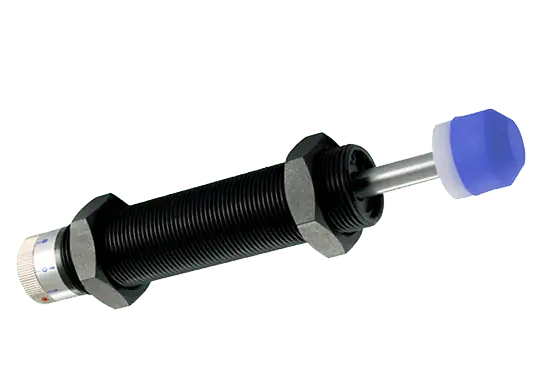
Pneumatic Shock Absorber
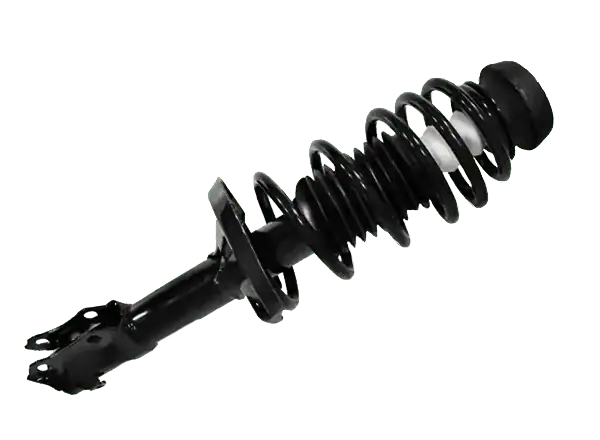
Gas-Charged Shock Absorber
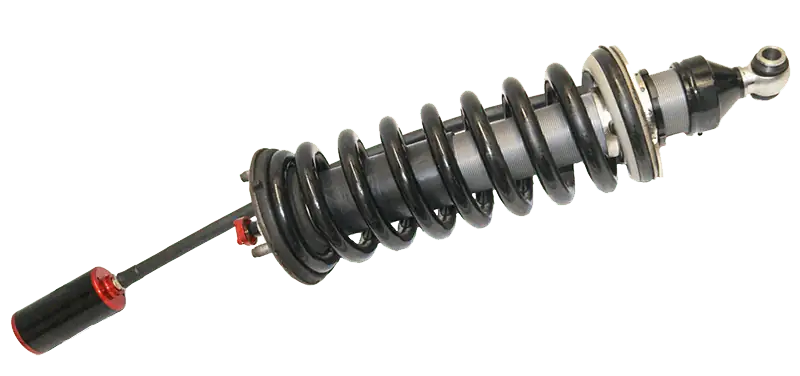
Electromagnetic Shock Absorber
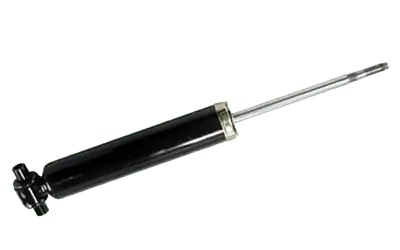
Monotube Shock Absorber
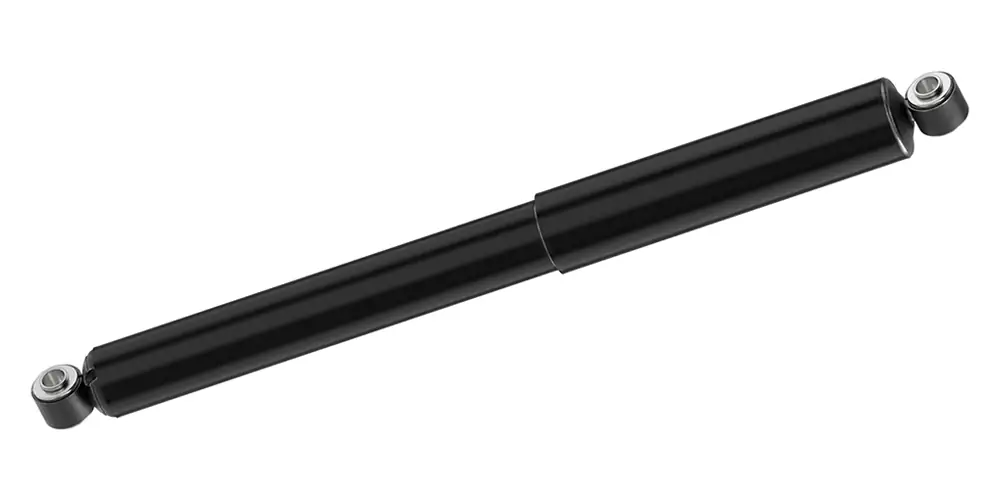
Twin-Tube Shock Absorber
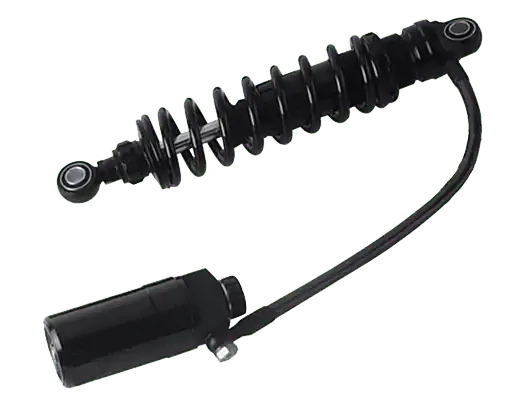
Remote Reservoir Shock Absorber
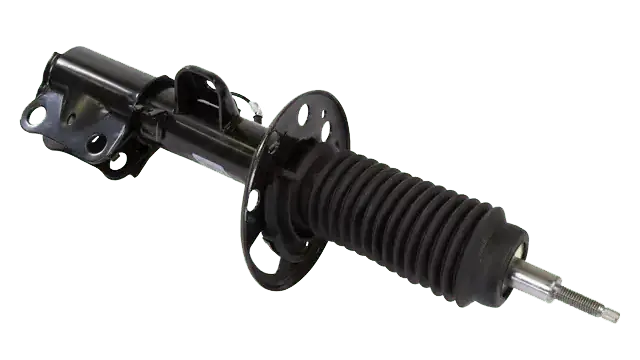
Strut Shock Absorber
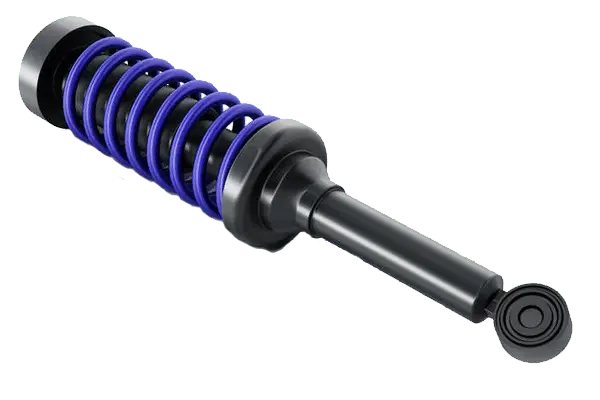
Separate Damper Shock Absorber
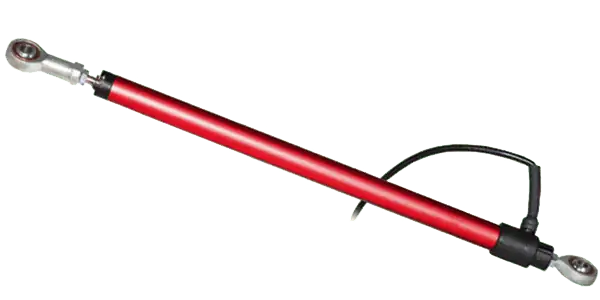
Linear Shock Absorber
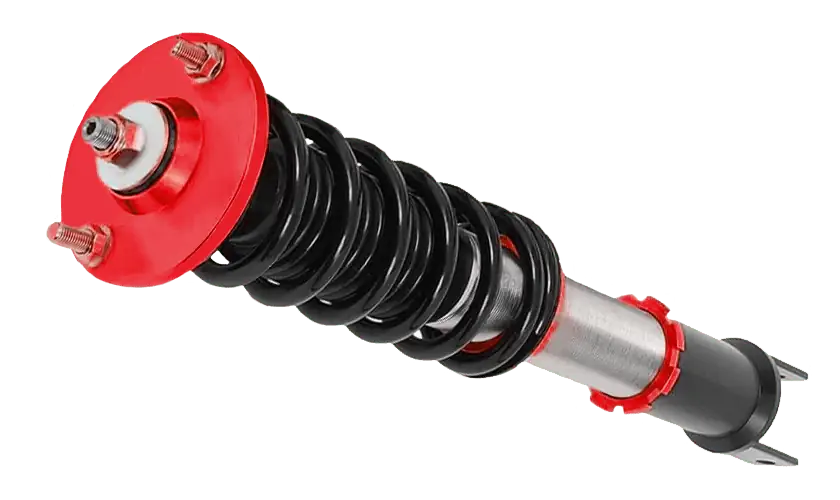
Digressive Shock Absorber
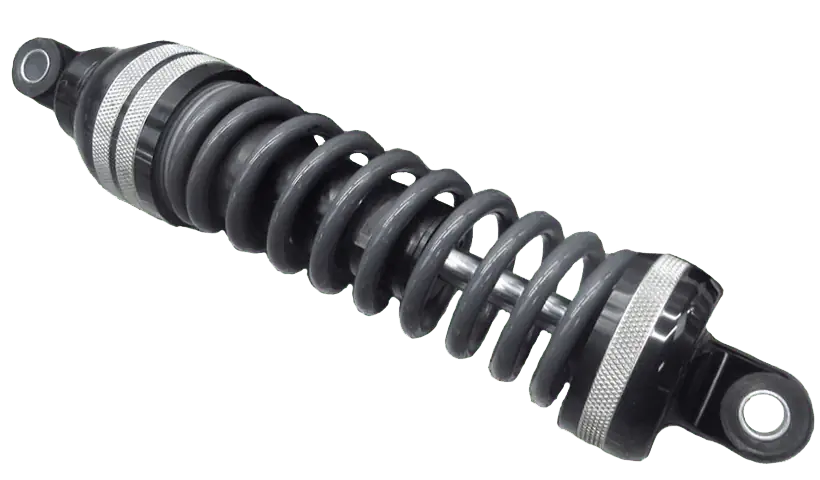
Progressive Shock Absorber
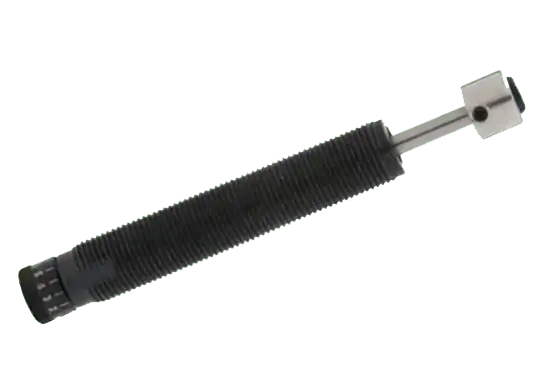
Non-Adjustable Shock Absorber
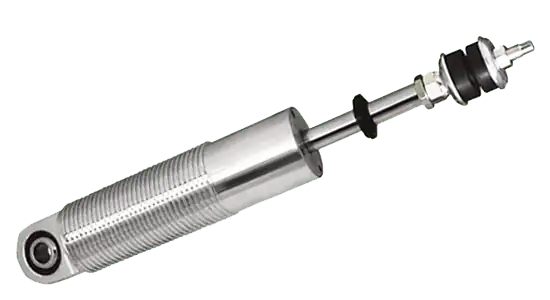
Rebound Adjustable Shock Absorber

Compression & Rebound Adjustable Shock Absorber
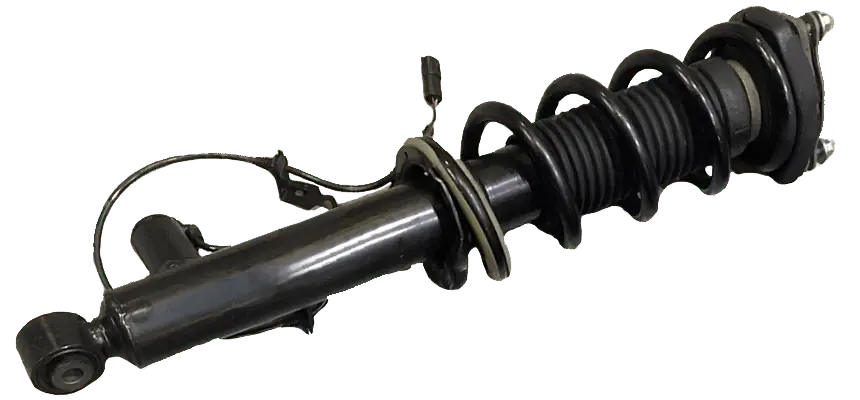
Adaptive (Active) Shock Absorber
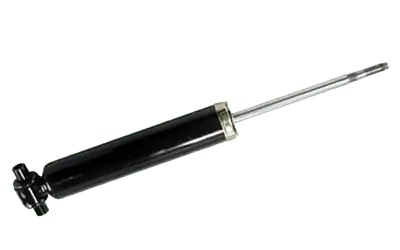
Passenger Car Shock Absorber
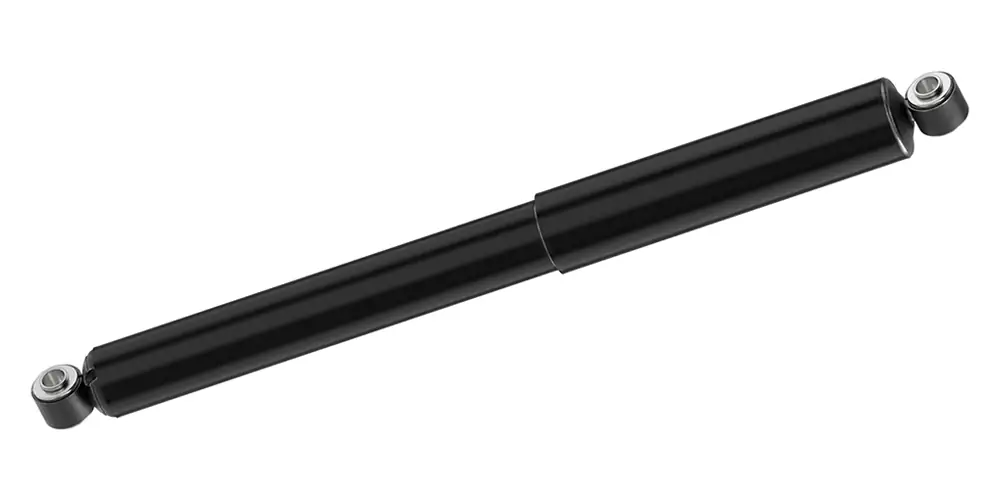
Commercial Vehicle Shock Absorber
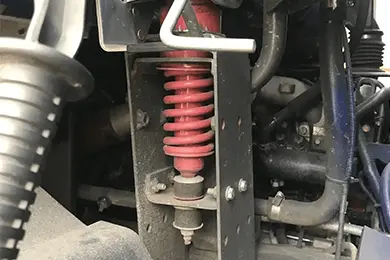
Construction Vehicle Shock Absorber

Motorcycle Shock Absorber
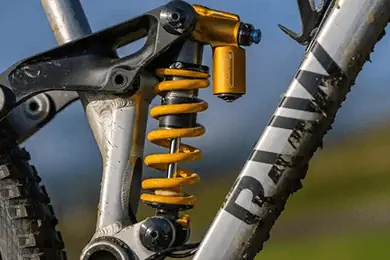
Bicycle Shock Absorber
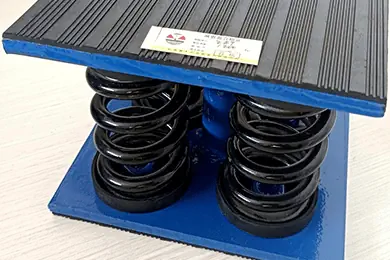
Industrial Machinery Shock Absorber
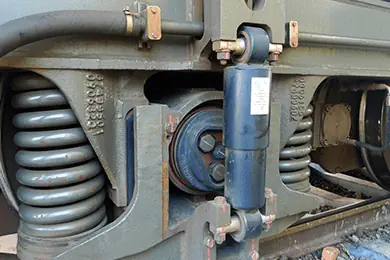
Railway Vehicle Shock Absorber
Automotive Shock Absorber Solutions | new energy · intelligent · lightweight
Multi-link shock absorber
Suitable for SUV/MPV models, lateral stiffness increased by 30%
Electromagnetic adjustable damping technology
Millisecond-level response (<0.1s) for real-time road adaptation. Ideal for autonomous driving and intelligent suspension systems.
New energy vehicle exclusive design
Using carbon fiber composite, 40% lighter weight with 5-8% extended range
Customized Shock Absorbers for Extreme Environments · High Safety Applications
Military-Grade Corrosion Protection: Withstands 1000-hour salt spray test (10-year coastal corrosion equivalent), compliant with GJB150.11A military standard.
Ultra-low temperature hydraulic oil formula: -50℃ viscosity index > 180, to ensure the stable operation of polar research equipment.
Explosion-proof certification buffer device: ATEX/IECEx dual certification, used for oil drilling platform, chemical plant explosion-proof area.
5 Proprietary Suspension Technologies Setting Industry Standards
1. Precision forging process
Switzerland + Japan composite production line: using cold forging + warm forging composite process, metal grain size up to ASTM 12, structural density increased by 40%.
2. Intelligent damping control system
Based on multi-sensor fusion, the system monitors pressure, temperature, and acceleration in real time, automatically adjusting valve opening. Achieves 92% vibration reduction in 8-stage dynamic tests.
Measured data: in the 8-level random vibration test, the amplitude is reduced to 1/3 of the competitive product.
3. Nano-coating technology
Double layer PVD coating: the surface friction coefficient is as low as 0.08, and the wear resistance is improved by 3 times.
Industry breakthrough: medical linear accelerator rail buffer, achieve 10 years maintenance-free.
4. Multi-physical field simulation system
Deep application of ANSYS: simulation of vibration, heat, fluid multi-field coupling, failure threshold increased by 65%.
5. Green intelligent manufacturing system
Full life cycle carbon tracking: from raw material procurement to finished product transportation, the carbon footprint is reduced by 28%.
Environmental certification: all products meet RoHS/REACH standards, heavy metal content is less than 0.1%.
OEM Quality Control: core guarantee to eliminate procurement risk
Raw Material Traceability
Sourced from Top 5 global steel suppliers (Baosteel, POSCO), with SGS-verified tensile strength ≥ 1200MPa and full batch certification.
Fully automated testing
Germany Carl Zeiss CMM: size tolerance control in ±0.01mm, interchangeability 100% qualified.
MTS hydraulic test bench in the United States: 100% passed 500,000 fatigue tests, and the data was uploaded to the cloud in real time for traceability.
After-sales service system
Long warranty: 12-36 months warranty, lifetime spare parts support (stock SKU 5000+).
48-hour emergency response: service centers in Asia, Europe and the United States, faulty parts will be replaced within 72 hours.
Shock Absorber Case Studies: Real-World Solutions for Global Clients
Case 1: Body roll Angle optimization project of German luxury car company
Solution: Customized magnetorheological shock absorber, built-in 32-section damping adjustment algorithm.
Results: The roll Angle was reduced to 2.8°, and the “Best Supplier of 2022” was awarded, and the order volume increased by 300%.
Case 2: Cold-resistant retrofitting of trucks in Siberian mines
Challenge: Standard shock absorber oil solidified at -45°C, causing downtime losses of $1.2M/month.
Solution: Developed ultra-low temperature fluorinated hydraulic fluid with <3000cP starting viscosity.
Result: Enabled 8,000 hours of continuous operation, achieving 100% repurchase rate.
Customized Shock Absorber Development Process: 4 stages to ensure accurate delivery
Stage 1: Requirements Diagnosis (3 working days)
Field mapping: 3D laser scanning equipment installation position, accuracy 0.02mm.
Vibration spectrum analysis: 0-2000Hz vibration data were collected to identify resonance frequency points.
Stage 2: Scheme design (5-10 working days)
Prototype testing: third-party laboratories issue CNAS certification reports (such as SGS, TUV).
Stage 3: Preparation for mass production (15 working days)
Mold development: Japan Makino high speed machining center, mold life of more than 500,000 pieces.
Process capability verification: CPK≥1.67, defect rate < 200PPM.
Stage 4: Continuous optimization (full life cycle)
Technology upgrade: Free annual iteration plan
Certifications & Global Distribution Network
Matrix of authentication
Quality system: ISO 9001, IATF 16949, GJB 9001C (military industry).
Product certification: CE, UL, DOT, ATEX, CCS classification society.
Environmental standards: RoHS, REACH, China Environmental label certification.
Global logistics network
Layout of bonded warehouses: Ningbo (Asian hub), Shenzhen (cross-border e-commerce channel), Hamburg (European center).
Customs clearance advantage: AEO advanced certification enterprise, customs clearance time increased by 50%.
Risk protection: covered by Ping An/Allianz Insurance, full compensation for cargo damage.
FAQ
① Request to provide CNAS test report;② Field visit to intelligent factory (support VR live preview); ③ Request similar project acceptance slip.
Using flexible production lines, MOQ 100 pieces still guarantee the whole process of quality inspection (has served 85 start-ups).
To solve oil leakage issues in shock absorbers:
① We use Freudenberg lip sealing rings from Germany;
② Each unit passes a 30MPa air-tightness test;
③ Oil spill guarantee policy available upon request.
High frequency damper (frequency range 5-2000Hz) + inertial mass block design is recommended, and the measured vibration reduction efficiency is > 90%.
① Establish customer exclusive ID, one-click query production/quality inspection records; ② The spare parts warehouse in Europe and America will arrive within 48 hours.
Listen to our clients how to saying about us
You will quickly understand our capabilities from our clients’ reviews.
They have excellent shock absorption resulting in increased customer satisfaction. MIVO’s products consistently meet and exceed expectations in terms of quality. Timely delivery and safe packing.
MIVO’s shock absorber makes a significant difference in ride quality. They handled the road irregularity well. Customer support is helpful in the buying process. Whenever I had questions about the technical aspects, the MIVO team responded quickly and provided clear answers.
Installation was simple and we were impressed by MIVO’s quality standards. It is clear that they care about the needs of their customers. In addition, including the after-sales service is excellent, if we have any questions, they are always ready to help us.