Stabilizer Links
MIVO – Professional Stabilizer Links Manufacturer specializing in Japanese, German, French, and American vehicles.
Explore our OE‑quality sway/stabilizer bar link solutions for improved handling and ride comfort.
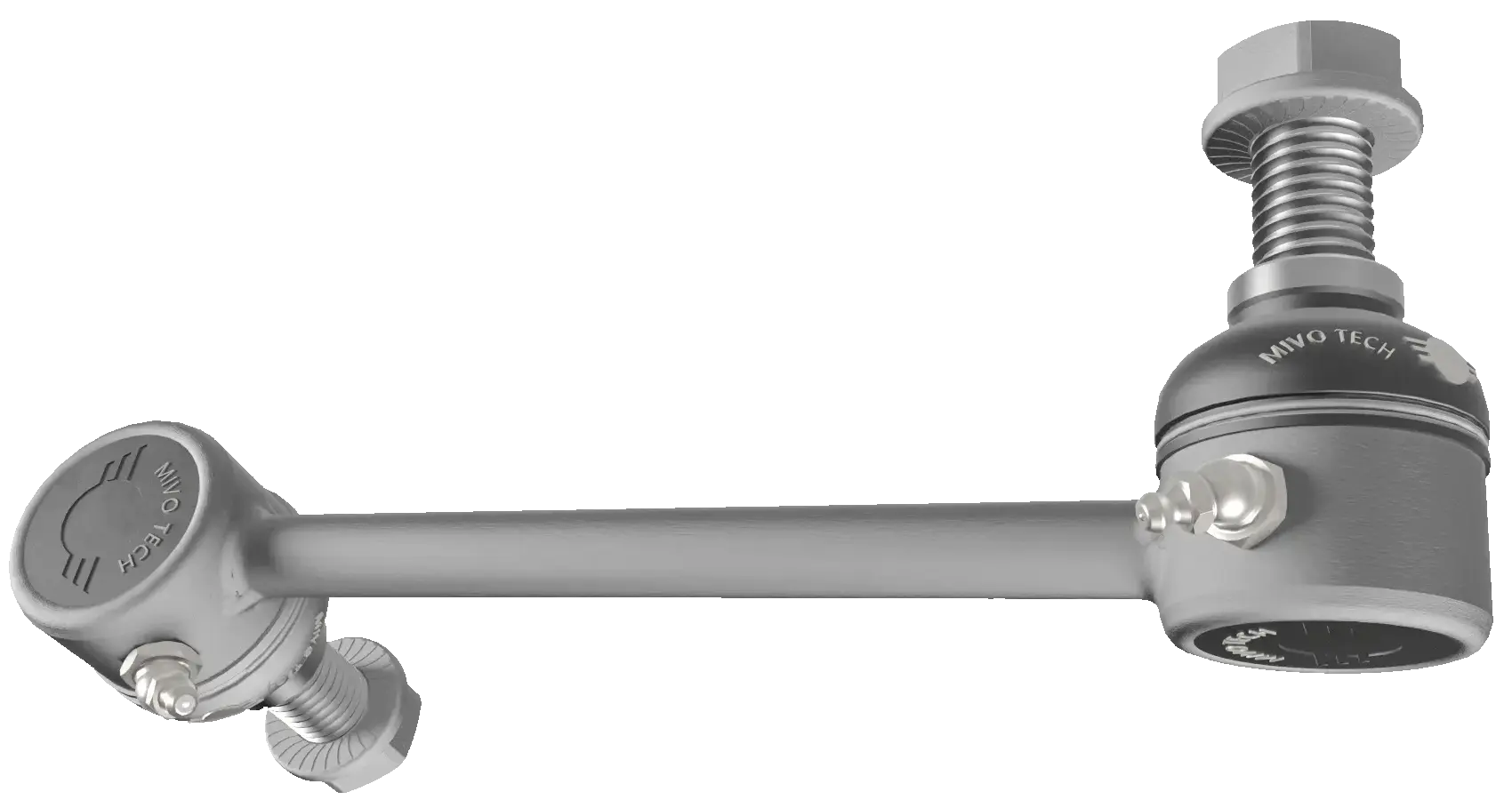
Types of Stabilizer Links & End Links
-
Rear stabilizer link
Links the rear anti-roll bar to the suspension, improving stability and traction. Usually longer with stronger construction for higher loads.
-
Front stabilizer link
Connects the front anti-roll bar to the suspension, reducing body roll when cornering. Typically shorter with single ball joint design.
Top Stabilizer Links Manufacturer in China | ISO 9001 Factory
As a professional Stabilizer links manufacturer in China, Mivo provides cost-effective and reliable suspension solutions to global customers through material innovation, intelligent manufacturing and strict quality control. Whether OE matching, after-sales replacement, or high-end customization needs, we can help partners win the market with technical strength and efficient service.
1.Cost and efficiency advantages
Factory direct supply mode: excluding the middleman mark-up link, the price is 30%-45% lower than the market price.
Fast delivery capability: automatic production line runs 24 hours, regular orders are delivered in 7 days, urgent orders are expedited in 72 hours (air support).
2.Technical research and development strength
15 years of experience team: The core engineers come from Uniform with 20 years of experience and have accumulated 12 patents for suspension systems.
3. Commitment to sustainable development
MIVO factory constantly introduce new equipment, new technology, to provide you with high value-added services while providing product quality.
Stabilizer links Ultimate Guide |
Professional Manufacturer direct OEM solutions
MIVO-25 years of focus on automotive suspension system components research and development manufacturing | ISO 9001 certified factory | global 300+ brand cooperation cases.
Reply within 2-8 hours
Via E-mail
MIVO sales and technical teams provide service 24/7
- 1.What is a Stabilizer link ?
- 2.Key Benefits of Stabilizer Links
- 3.Product Types & Application Scenarios
- 4.Stabilizer Link Material: Steel, Aluminum & Titanium for EVs
- 5.Surface Treatment & Corrosion Protection
- 6.Precision Manufacturing & CNC Tolerances
- 7.Testing & Validation
- 8.International Certifications & Quality Standards
- 9.Full‑Process Quality Control & After‑Sales Support
- 10.MIVO Advantage Services: Global Fitment & Rapid Prototyping
- 11.Installation & Replacement Guidelines
- 12.In-depth analysis of common problems of Stabilizer link
1. what is stabilizer bar link ?
Stabilizer link is the core component of automobile suspension system. By connecting Anti-Roll Bar and suspension system, it realizes the transfer and buffer of body roll torque.
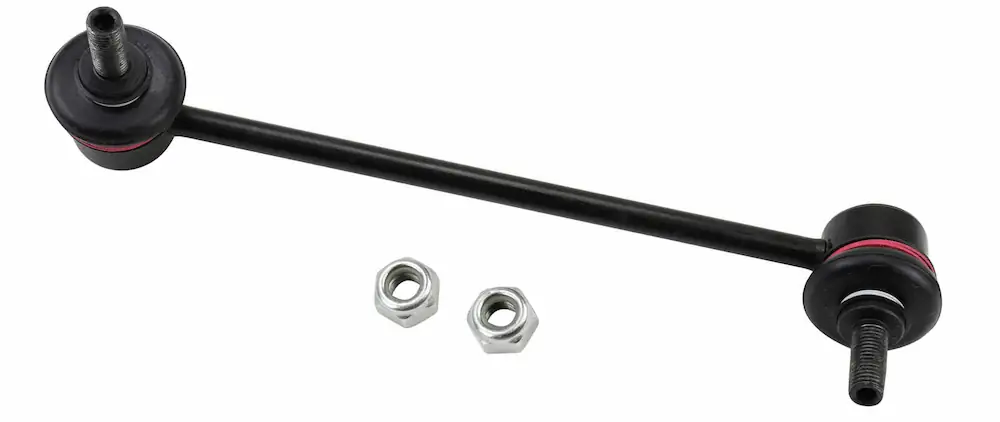
2. Key Benefits of Stabilizer Links (Sway Bar End Links)
Roll control: When the vehicle turns, it reduces the body tilt by 30%-50% (NHTSA test data) through the mechanical lever principle, and improves the stability of cornering.
Tire grip optimization: By balancing the dynamic load of the suspension system, it ensures the maximum contact area between the tire and the road surface and reduces the risk of skid.
Driving comfort improvement: the rubber bushings and ball head structure are used to absorb more than 80% of irregular vibration, reducing the impact of bumpy road conditions.
3. Product Types & Application Scenarios
Single section: simple structure, suitable for ordinary passenger cars and economy aftermarket, low cost.
Double pitch (double ball head design) : larger movement Angle (±45°), suitable for complex road conditions and high load scenarios, such as off-road vehicles, construction machinery and modified racing cars.
New energy vehicles: for the lightweight requirements of electric vehicle chassis, aluminum alloy and titanium alloy materials are used to reduce weight by more than 30%.
Commercial vehicles: To meet the high load requirements of heavy trucks and buses, the rod thickness and welding process are strengthened to increase the carrying capacity to 5 tons.
Race modification: Provide customized high stiffness solutions for racing cars, supporting extreme working conditions with instantaneous lateral acceleration ≥1.5G.
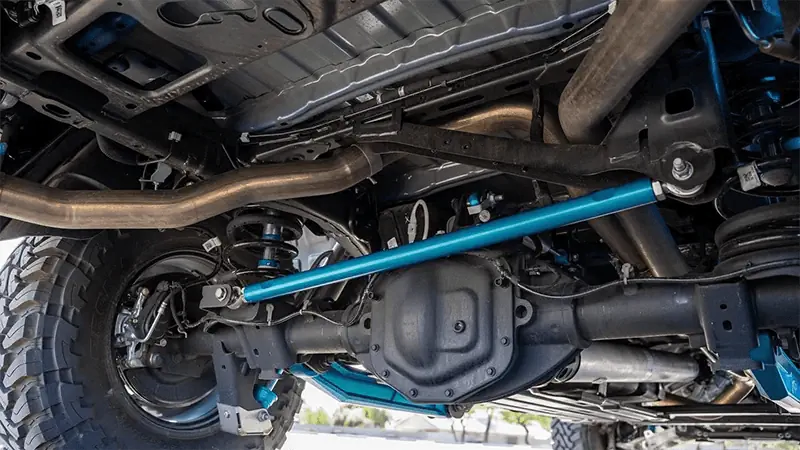
4. Stabilizer Link Material: Steel, Aluminum & Titanium for EVs
SAE J2340 ultra high strength alloy steel: tensile strength ≥1200MPa, yield strength up to 900MPa, far beyond ordinary carbon steel (below 500MPa), to ensure that the rod body does not deform in high frequency vibration.
Titanium alloy forging process: using cold forging technology, improve metal compactness, fatigue life of more than 2 years, suitable for desert high temperature and extremely cold environment.
5. Surface Treatment & Corrosion Protection
Galvanized layer (8-12μm) : no rust through salt spray test for 1000 hours, suitable for coastal high humidity areas.
PTFE self-lubricating bushing: friction coefficient as low as 0.05, achieving a maintenancy-free design, reducing the frequency of grease change by 80%.
6. Precision Manufacturing & CNC Tolerances
CNC machining accuracy: the ball head and rod body are processed by five-axis linkage CNC machine tool, and the tolerance is controlled at ±0.01mm to ensure seamless compatibility with OE components.
7. Testing & Validation
Fatigue test: simulate 500,000 cycle loads (equivalent to 300,000 kilometers of vehicle driving), far exceeding the industry standard of 300,000.
Low temperature test (-40℃) : to verify the elastic recovery ability of rubber bushings under extreme cold.
High temperature endurance test (120℃) : ensure the stability of coating and bushing in desert environment.
Dynamic balance test: vibration amplitude ≤0.1mm at 3000rpm to avoid resonance problems in high speed driving.
8. International Certifications & Quality Standards
IATF 16949: the highest quality management standard in the automotive industry, covering the whole life cycle management from design to delivery.
REACH/SVHC: Ensure zero detection of 205 hazardous substances in materials, in accordance with EU environmental regulations.
TUV Rheinland certification: passed dynamic load and vibration tests, endorsed by a German laboratory.
9. Full‑Process Quality Control & After‑Sales Support
Raw material testing: X-ray fluorescence spectrometer (XRF) was used to analyze the alloy composition to ensure that the material complies with SAE J2340 standard.
Process monitoring: real-time data (such as welding temperature and coating thickness) is collected for each key process, and abnormal warning is realized through MES system.
3D coordinate measurement: accuracy ±0.01mm, ensure 100% qualified size.
Technical support: Provide 3D models (STEP format) and CAD drawings for free, support SolidWorks/UG/CATIA multi-platform compatibility.
Marketing empowerment: professional photography team to take product pictures, and provide English, French, German, Spanish language manual template.
After-sales guarantee: non-human damage within 3 years free replacement, provide global 48 hours emergency spare parts allocation service.
10. MIVO Advantage Services: Global Fitment & Rapid Prototyping
- Extensive Model Coverage: • 2000+ global vehicle models in our database (Europe, America, Japan, Korea) • Precise OEM part matching for passenger cars, SUVs, trucks and EVs
- EV & Hybrid Solutions: • Lightweight titanium alloy links for Tesla Model Y, BYD Han, etc. • Weight reduction up to 35% without compromising strength
- Fast Custom Prototyping: • 3D scanning & reverse engineering from your samples or drawings • Prototype delivery within 3 business days for rapid validation
- One‑Stop OEM Support: • CAD/STEP files & technical drawings provided free of charge • Dedicated project manager for streamlined communication

11. Installation & Replacement Guidelines
- Preparation:Confirm the model, clean the installation position, and check the wear condition of the rubber lining and ball joint .
- Disassemble old parts:Use a suitable wrench or special tool to loosen the lock nut first, and then use a ball joint separator to detach the ball joint.
- Install new parts:Insert the new stabilizer bar link ball head into the bracket and tighten the nut by hand to the reference position.
- Tightening precautions:Refer to the torque values in the vehicle maintenance manual, or have a professional technician perform final calibration after installation.
- Test drive inspection:Test drive at low speed and on bumpy roads to confirm no abnormal noise or looseness.
(For specific torque, please refer to the maintenance manual or OEM specification table of each vehicle model)
12. In-depth analysis of common problems of Stabilizer link
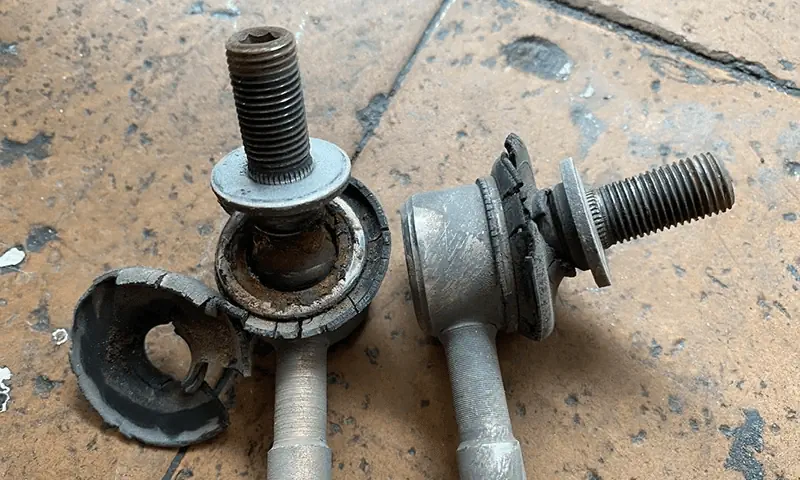
1).Replacement time and detection method
Classical symptom
Chassis abnormal sound during bending (metal collision sound) : ball head wear leads to excessive clearance.
Steering wheel virtual position (steering delay) : the stiffness of the connecting rod decreases, and the torque cannot be effectively transmitted.
Professional testing tools:
Use a digital torque wrench to measure the rotational resistance of the ball head. The standard value is 1.5-3.5N·m. If it is lower than 1.2N·m, it should be replaced immediately.
2).Mistakes and suggestions on the selection of modified vehicles
Misconception: The blind pursuit of high rigidity leads to excellent suspension and affects comfort.
Solution
Select stiffness according to vehicle use: track car can be increased to 400kN/m, daily modification is recommended 250-350kN/m.
With adjustable bushing, dynamic balance control and comfort.
3).Guidelines for climate adaptive maintenance
High humidity area: check the tightness of the dust jacket every 6 months to avoid the corrosion of the ball head caused by mud intrusion.
Extreme cold areas: use -60℃ low temperature grease (such as Mobilith SHC 100) to prevent busings from hardening and cracking.
Desert environment: Install nylon dust cover (IP67 protection grade) to prevent sand abrasion.
Listen to our clients how to saying about us
You will quickly understand our capabilities from our clients’ reviews.
The Stabilizer Link of MIVO can effectively reduce the body roll and improve the control. The order flow was smooth and the delivery was on time. MIVO’s efficient supply chain management ensures that they can meet our needs in a timely manner.
In our repair shop, the stabilizer link from MIVO was a great help. I would be happy to recommend these products. Whenever we encounter any technical issues with our products, the MIVO technical team is always available to provide timely solutions.
The stabilizer link of MIVO improves the stability of my vehicle and makes the ride smoother. At the same time, their commitment to customer satisfaction is evident in their handling of after sales inquiries and providing the necessary support I think is impeccable.